Schrott Auffangeinrichtung für EAF Quantum Elektrolichtbogenofen
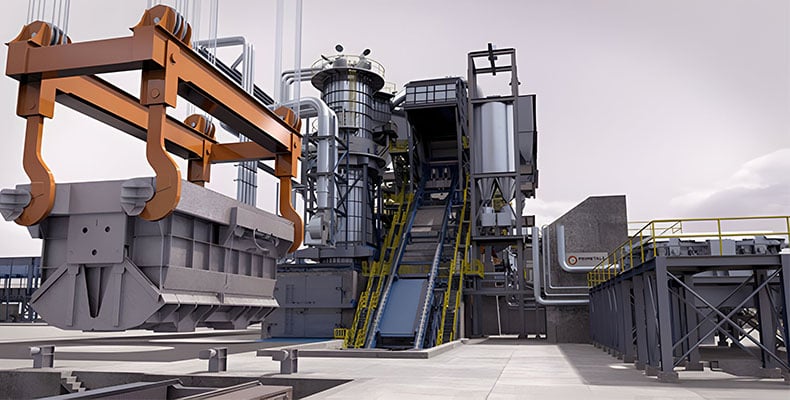
In der energieintensiven Stahlherstellung setzt Primetals mit dem EAF Quantum Ofen neue Maßstäbe für Nachhaltigkeit. Durch innovative Technologie und ein integriertes Heizsystem zur Verarbeitung von Stahlschrott wird nicht nur der Energieverbrauch minimiert, sondern auch CO2-Emissionen reduziert. Erfahren Sie mehr über diese wegweisende Lösung für eine umweltbewusste Stahlindustrie.
In diesem kann Stahlschrott in sehr unterschiedlicher Zusammensetzung und Qualität verarbeitet werden. Im Vergleich mit konventionellen Elektrolichtbogenöfen ist der Bedarf an elektrischer Energie hier äußerst gering, weil unter anderem der Schrott durch ein integriertes Heizsystem vorgewärmt wird. Das senkt sowohl die Betriebskosten als auch die CO2-Emissionen. In Kombination mit dem reduzierten Elektroden- und Sauerstoffverbrauch ergibt sich ein Gesamtvorteil von rund 20 % bei den spezifischen Umwandlungskosten. Insgesamt können die gesamten CO2-Emissionen im Vergleich zu konventionellen Elektrolichtbogenöfen um bis zu 30 % pro Tonne Rohstahl reduziert werden. Der Metallschrott wird in einen Container geladen, der Teil eines automatischen Schrottbeschickungssystems am Boden des Ofens ist (Bild 2). Der Behälter wird auf die Oberseite des Ofens gehoben, wo er entladen wird (Bild 3).
Der Schrott fällt aus großer Höhe auf das Schrottrückhaltesystem (Bild 4). Dieses liegt direkt über der Schmelze, durch deren direkte Abwärme und ein Wärmerückführungssystem der Schrott vorgeheizt wird. Es besteht aus jeweils 6 sich gegenüberliegenden Fingern (Bild 5), an deren äußeren Enden jeweils ein Puffer mit RINGFEDER® Reibungsfedern installiert ist. Wenn der Schrott eine Temperatur von 600°C erreicht hat, öffnet sich das Fingersystem und er fällt in die Schmelze. Die Puffer bringen Flexibilität in das System und schützen es vor Beschädigungen, wenn die durch den auftreffenden Schrott entstandene Fallenergie freigesetzt wird.
Zu Beginn des Projekts war noch nicht endgültig definiert, wie groß die Masse sein würde, die bei jedem Absetzvorgang auf die Finger trifft. Aus diesem Grund wurden anfangs Dämpfer mit einer Einzelfeder vom Typ 24201 mit einer Maximalkraft von 1000 kN konstruiert. Die Diagrammwerte hätten eine maximale Betriebslast von 740 kN bei einem Federweg von 62 mm, einer Vorspannung von 100 kN und einer Kapazität von 47.500 Joule ermöglicht. Zudem wurden sie so ausgeführt, dass nachträglich zusätzlich parallel geschaltet eine Feder vom Typ 19600 hätte eingebaut werden können, falls die freigesetzte Energie höher werden sollte als ursprünglich kalkuliert. Nach weiteren Berechnungen zeigte sich dann, dass die tatsächlich benötigte Energieaufnahme deutlich geringer ausfällt. Die endgültige Version enthält die Reihenschaltung der genannten Typen 24201 und 19600, was dazu führt, dass die Kennlinie in Absprache mit dem Kunden im Diagramm einen geknickten Verlauf vorweist.
Das System hat sich bewährt und wir stehen unserem Kunden mit diesem Produkt seit 2013 als Partner zur Seite. Dies zeigt einmal mehr, dass RINGFEDER® Reibungsfedern in verschiedensten Umgebungen bei extremen Bedingungen zum Einsatz kommen können.
Kommentieren