Industry 4.0: Why robots cannot replace engineers
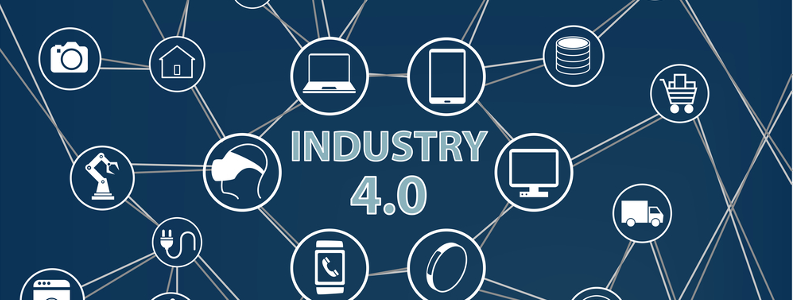
One of the most discussed topics in mechanical engineering but still it is hardly tangible for many companies and engineers. This is most likely due to the fact that the idea behind the so called forth industrial revolution is well-known, but there exist many different opinions and approaches when it comes to the implementation. We want to have a closer look at the current situation in the market.
Even though Industry 4.0 is often considered as a marketing term, it cannot be denied that this future-oriented project and the idea of the ‘smart factory’ have managed to establish themselves in manufacturing industries during the last years. Some companies have taken first steps – towards a comprehensive use of intelligent systems and accordingly towards an optimization of the supply chain.
Thus, the vision of the Internet of Things (IoT) emerged, based on cyber-physical systems (CPS) and a constantly improving connectivity between devices. This should enable the systems to take decisions and to initiate actions without human intervention or to offer the best possible support for the user in a first step.
ABB Group, for example, developed a smart sensor for low voltage induction motors, which is collecting data to be analyzed via software and finally providing information on maintenance requirements. This is a best practice in terms of intelligent technologies for human-machine interaction.
Based on this analysis, actions can be initiated if needed to minimize costs and to reduce down times. Thereby this technology offers high potential for cost savings when it comes to maintenance and repair and furthermore enables the operator to influence one of the significant key factors for success in today’s production industries.
Does technology isolate or connect the smaller ones?
Apart from these measures especially small and medium-sized companies face the challenge that this industrial development will have a lasting effect on the entire world of work, on organizational cultures and on demands on employees. There are concerns that humans could be replaced by machines and increasing complexity of software as well as changing IT systems may lead to uncertainty or in some cases to a negative view.
Some smaller companies consider the topic as irrelevant, others see a lack of specialists and high investment costs as obstacles. John Horn, CEO of Ingenu, explains in detail why IoT is important and beneficial for small businesses. Experts assume that companies still have time for strategic decisions but considering a period of ten years the implementation of a smart production will be essential.
It is never too late to learn
In the end, the demands on individualization will be pushed by the market itself. Production should be optimized so that even small lot sizes can be produced profitably. Substantial benefits include better networking throughout the entire supply chain as well as improvements in quality by constant control. Equally relevant are cost saving potentials with regard to maintenance by ‘foresighted’ machinery. So there are no reasons for rejecting to participate in this development.
Even though there was recently a lot of talk about an massive decrease in employment which will go along with Industry 4.0, the producing industries will further rely on the human element. Despite the fact how mature processes are, whether robots will control production and which additional capacities will be created within product development, the scenario of an unmanned factory seems to stay a vision. Especially engineers will be in demand further on, however with new priorities while working in interdisciplinary and international teams: besides knowledge about mechanical engineering, extensive software skills, soft skills, intercultural competence and language skills will become more and more important.
In general the prevailing opinion is that the manufacturing industries will be less affected than healthcare industries and the financial sector. Still it is more than likely that requirements on the quality of work and skills will change, especially when it comes to flexibility. This means that early investments in training of staff are needed to develop a capable and qualified team.
Furthermore companies should develop a long-term strategy also considering their customers’ demands. A pilot project could be a good start and also an exchange of ideas and experiences with business partners and suppliers can be of good help. Then the challenges of this forth industrial revolution can be turned into success. More interesting reports on reference projects can be found on the Fraunhofer-Institutes' website.
Glossary
Industry 4.0
also referred to as the fourth industrial revolution, it describes the idea of a smart factory and deals with the digitalization of production considering artificial intelligence, rising data volume and the Internet of Things.
Internet of Things (IoT)
The Internet of Things (IoT) is a system of interrelated computing devices, mechanical and digital machines, objects, animals or people that are provided with unique identifiers and the ability to transfer data over a network without requiring human-to-human or human-to-computer interaction.
Cyber-Physical Systems (CPS)
Cyber-Physical Systems are integrations of computation, networking, and physical processes. Embedded computers and networks monitor and control the physical processes, with feedback loops where physical processes affect computations and vice versa.
Comment