From the Invention to Earthquake Protection – the History of the RINGFEDER® Friction Spring
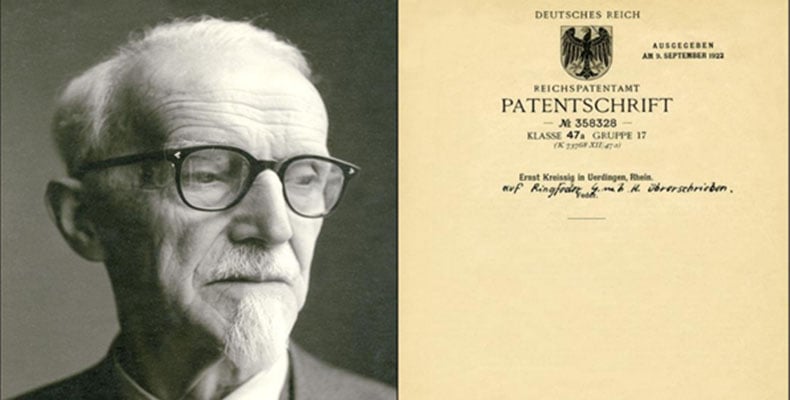
The history of the RINGFEDER® friction spring goes way back: from the first patent application, use in train bumpers, truck trailer couplings, and landing gears systems of airplanes up to advanced earthquake protection. Learn more about the most important milestones in this article.
Invented more than 100 years ago
Looking at a RINGFEDER® friction spring you would not assume that this damping element was invented more than 100 years ago. In fact, Dr. Ernst Kreissig, the founder of the company RINGFEDER, had his first patent application rejected. Unfortunately, the patent official had not fully understood the functionality and the principle of energy absorption on account of elastic deformation of steel parts.
Finally, on September 9, 1922, a successful second patent attempt resulted in the granting of patent number 358328. This also led to the foundation of the company RINGFEDER on December 4, 1922.
The original idea was to use friction springs as buffer elements between the wagons of railway trains. This was a genuine innovation, because simple wooden bumpers had been used since the 1830s, e.g., for the legendary locomotive „Adler”. These wooden bumpers were not replaced by rod bumpers until around 1905.
Wooden bumpers of the replica of the “Adler” locomotive (source: https://de.wikipedia.org/wiki/Puffer_(Bahn); Urmelbeauftragter; CC BY-SA 3.0)
From the thin rod buffer to…
Historically, rod buffers consisted of rods with buffer plates at the front end. At the other end, the rod was movably mounted on a spiral volute spring which was supported by a solid sheet metal sleeve.
As the rod buffers often suffered deformation in service and/or caused great damage in accidents, the plunger buffer was developed as an alternative. These buffers featured a buffer plate that sat on a steel tube with a larger diameter. This made the plunger buffer more resistant to bending.
Rod buffer with volute spring (Source: https://de.wikipedia.org/wiki/Puffer_(Bahn); Christian Lindecke; CC BY-SA 3.0)
… plunger buffers with volute spring system
However, the volute spring system initially still used in plunger buffers had the difficulty of fully releasing the absorbed energy when it was compressed, so that the vehicles were pushed apart again after the impact. Therefore, the trains always had to be braked uniformly, and not at selective points, to avoid vibrations in the train set which could cause the couplings to break.
Friction springs provide many benefits
A substantial improvement was then achieved by the use of RINGFEDER® friction springs, because they were able to convert most of the induced energy into frictional heat instead of transferring it back to the adjacent structure. This is why friction springs are still mounted to some train buffers today.
Success was not long in coming: the business expanded internationally shortly after the foundation. Thanks to the high efficiency of the friction springs, the first license agreement was placed with the US enterprise Edgewater Steel Company based in Oakmont, Pennsylvania, in the year 1924. This collaboration appeared evident as the American company founded in October 1916 specialized in the manufacture of forged and rolled products for the transport industry.
Establishment of a rolling mill in France
1927 saw the establishment of a rolling mill in France, and in 1928, Ringsprings Ltd. was launched in Great Britain. Although business was excellent, Dr. Kreissig had the foresight at that time not to rely on just one business area.
So he looked for other application areas to establish a broader foundation for his company. In this he benefited from the fact that there were, and are still today, numerous applications in all industries where large motion energy has to be absorbed and damped, or applications where springs are required to take up large forces within compact spaces.
The first successful innovation was achieved in 1930 with the development of a trailer coupling for trucks; this coupling celebrated its official premiere on the IAA in 1935. The landing gear systems of many airplanes were also equipped with RINGFEDER® friction springs to absorb the energy during the landing procedure, thus protecting the structure of the aircraft. The Junkers Ju-52 is probably one of the most famous aircraft to use the RINGFEDER® friction spring.
Conquering new business areas
Up to the 1950s, the bulk of the business involved buffers for railway vehicles with a production capacity of 200,000 units per year. Then, slowly but surely, new developments emerged in railway technology so that the company again concentrated on capturing new business areas.
These endeavors were and have been successful up to date. The application possibilities for RINGFEDER® friction springs are endless: from the conventional application as end stops in steel plants, to mass dampers in antenna masts or as safety devices to protect gearboxes against overload while adjusting the landing flaps of airplanes. They also help protect residential buildings and industrial plants against damage caused by earthquakes.
When design philosophies change
To be precise, RINGFEDER POWER TRANSMISSION began to develop solutions for reliable earthquake protection more than 25 years ago. It started with friction springs as earthquake guarding of electric switches for AEG, and generator platforms for General Electric. However, the company's orientation towards the industrial sector had already advanced so far at that time that, although earthquake protection was considered a new and interesting business area, the focus was elsewhere.
This picture shows surge arrestors with 4 tension-compression devices and RINGFEDER® friction springs mounted as feet to provide more flexibility for the arrestor.
At that time, the design philosophy for earthquake protection was totally different compared to today. In order to make buildings resistant to earthquakes to the best possible extent, they used to be designed and built very rigidly. The prevailing premise was to protect the people inside buildings as much as possible. The fact that a building was destroyed during an earthquake, and hence could no longer be used, played a rather minor role. Today, however, no economy can afford this, as reflected in the table below showing the ten most expensive earthquakes for insurers.
The ten most important earthquakes for insurers (Sources: Munich Re (NatCatSERVICE) via Statista)
RINGFEDER® friction springs for effective earthquake protection
Nowadays, buildings should remain undamaged as far as possible during an earthquake. In addition, people should be able to continue living and working in them while the required repairs are being carried out at the same time.
This is especially true for critical infrastructures like hospitals, fire services, drinking water and electricity providers, etc. To achieve this and comply with contemporary requirements, an increased degree of flexibility is needed. At this point, the benefits of the RINGFEDER® friction springs can be realized: They make the affected systems more flexible, reliably absorb energy, and assist in the “re-centering” of buildings and structures to their original position after an earthquake.
These were the most important milestones. And it continues: In the next part of our article series, we will explain the function principle of RINGFEDER® friction springs.
Comment