Maintenance: Focus on couplings
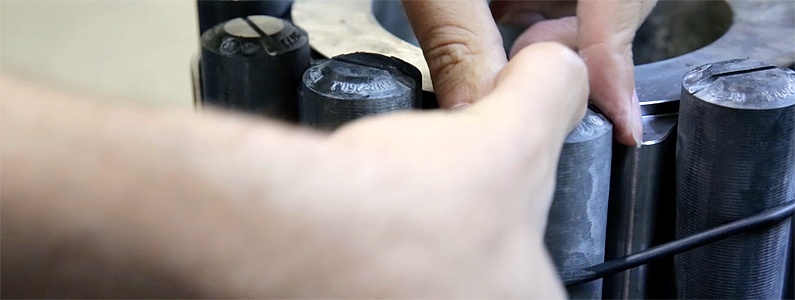
Couplings in drive lines are of particular importance because they transmit power between the input and output side, and compensate for inevitably occurring misalignments of the units. Like other machinery elements, couplings need to be serviced at regular intervals. Only if the coupling is optimally tailored to the requirements of the operating conditions and subject to regular maintenance, can it contribute to ensuring the operating reliability and efficiency of a machine or plant.
A survey conducted in Germany among companies operating in the fields of production, manufacturing, infra-structure, traffic and transportation showed that 72 percent of them deem downtimes of plants as having grave economic consequences. For large-scale plants it is 83 percent. If replacement parts are available in stock, downtimes – and hence costs – can be considerably reduced.
A basic rule applies: the larger the plant, the more important its continuous availability, and the more standards and regulations, e.g. occupational health and work safety , have to be complied with and implemented, the higher the costs are for maintenance and repair.
Stresses and strains in engine-driven plants
Besides the shaft-hub connections, transmission elements are the most stressed parts of couplings. Among these are compression loaded or shear loaded flexible and highly flexible elements, the disc packs of a steel disc coupling as well as the crowned teeth of gear couplings. They transmit the torque between the units. On account of their resilience, flexible couplings are able to compensate for torque shocks. Torsionally stiff couplings are less suitable for this.
In a compact design or designs with bell housings, temperatures may occur in the direct vicinity of the coupling which will cause the elastic elements to age faster.
In addition to the temperature, the frequency and intensity of torque shocks influence the lifetime of transmission elements. The optimum coupling design avoids premature wear. Calculation simulations such as torsional vibration analyses help select the optimum type of coupling. Such analyses should always be conducted for a drive line where dynamic excitations caused by a combustion engine are present.
Stiffness and Damping influence stresses and strains on the drive line
Vibrations due to torque shocks adversely affect the drive line. Stiffness and damping of the coupling influence the process. (Click on the picture to enlarge)
Plant-related processes and environmental influences can put additional load on the coupling, e.g. if scales enter the coupling during steel production. This can be avoided, if, for example, an enclosed coupling design is used.
If the plant operating conditions allow for an interruption of torque transmission, non-fail-safe couplings are appropriate solutions. If the elastic elements are worn, torque transmission will be interrupted without harming the metallic parts. In most cases, this will also prevent damage to the adjacent units.
Comment