Hydrodynamic Couplings in Bulk Material Handling Equipment Drives
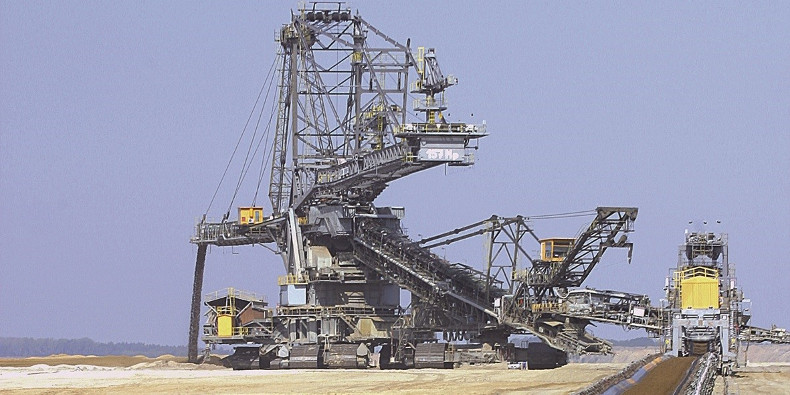
Bulk material handling is an engineering field that is centered on designing and manufacturing of special equipment utilized to handle mainly dry materials such as ores, grains, sand, gravel and stone in loose bulk form. Mineral production, for instance, depends on a great quantity of bulk material handling equipment in order to move an impressive portion of the iron and copper ore productions in the world. In the following we want to explain how hydrodynamic couplings operate and how they can improve the MTTR of bulk material handling equipment drives.
Daily Challenges
With Brazil being the second largest iron ore producer in the world, and Chile and Peru, being the first and second in copper ore, the daily challenges faced by these industries made them evolve throughout the years in order to keep up with the worldwide demand for these important commodities.
A combined production that reached over 447 million tons in 2017 requires consistent bulk material handling solutions to keep costs down and profits up, since excessively long and/or unexpected maintenance interventions could cause millions of dollars of financial losses.
Components in Drive Systems
When it comes to the installation, operation and maintenance of drive systems, components that allow a radial assembly and disassembly are an excellent alternative to reduce the MTTR (mean time to repair) and increase the production availability of such equipment, which is a key factor to increase profit.
Efficient solutions that can be applied to both, new and existing equipment, and which are based on the "radial assembly/disassembly" concept, make maintenance processes easier, faster and as reliable as any top notch solution available. In the following we would like to explain their specific features and benefits.
Starting up equipment with heavy masses
Iron and copper ore handling requires an equipment with very large capacities and consequently, high potency and inertia. Starting them up is not an easy task, considering the mass of the material contained in loaded condition and the mass of the equipment itself.
As a consequence, most of the drive systems are equipped with single or multiple electric motors that allow the startup to be processed in a short period of time. Considering that such startup characteristics can cause both, overheating and huge shocks to the system, increasingly hydrodynamic couplings are applied to aid the startup:
Based on the "Föttinger principle", a hydrodynamic coupling consists basically of two bladed rotors, being the pump rotor connected to the input shaft (motor) and the turbine rotor to the output shaft (gearbox). When assembled with a shell, it forms a chamber in which the fluid (mineral oil or water) is placed.
As you can see on the image below, the operating principle of a hydrodynamic coupling is quite simple:
The electric motor (left) sets the shell and pump rotor in motion (blue), since they are attached to the motor shaft. As it gains speed, the kinetic energy of the operating medium (mineral oil or water) inside the coupling increases and propels the turbine rotor (red), which is attached to the output shaft connected to the gearbox (right), gradually transmitting the torque to the equipment with a minor slip (2 to 4%) and no mechanical contact.
Please check the video to see the startup of a Pipe Conveyor with a hydrodynamic coupling.
Hydrodynamic Couplings
Since there is no mechanical contact between the motor and gearbox, the electric motor is not subjected to the load of the driven machine, even when loaded or stalled. This enables an immediate drop of motor start-up current, which contributes to electric energy savings. But there are a lot more advantages:
Smooth acceleration of heavy loads with no need to use overdimensioned motors
Normally, during start-up the maximum motor torque is required. When using a hydrodynamic coupling, the motor can be dimensioned based on the power actually required by the driven machine.
Limitation of the maximum torque
The coupling limits the maximum torque providing efficient protection of both, your motor and the driven machine.
Overload protection
In case of a driven machine overload, the output shaft connected to the coupling's turbine rotor may stall (100% nominal slip), however, the pump rotor connected to the input shaft will keep going at the nominal rotation.
Even load distribution
Among all motors in case of multiple drives. The start-up can be configured to occur in sequence, thus avoiding high peaks of power consumption.
Protectdion against overheating
In case of a prolonged stalling of the turbine rotor, a fuse plug is triggered emptying the coupling and thus interrupting transmission. It’s possible to use a thermo-eletronic device to monitor the temperature, turning drive set off at the maximum set temperature.
Wear free power transmission
Since there is no mechanical contact between the pump and turbine rotors.
High efficiency
Through protection of all electrical and mechanical drive elements, even when the rotation commutation/reversal occur with high frequency.
HENFEL Hydrodynamic Couplings
HENFEL, manufacturing and sales location of RINGFEDER POWER TRANSMISSION in Brazil, applies the same operating principles as shown above to its new generation of Hydrodynamic Couplings – the HENFLUID NG series.
The differences are the constructive form and the progressive fixation system: Couplings of this series allow a radial assembly / dissassembly, so that the mounting and dismounting can be completed significantly faster – without necessity to move components of the drive system, as this is required with other fixation systems. Watch our video:
NG series can also be manufactured customer-specific to be interchangeable with other internal and external fixation models.
Summary
In short, external fixation hydrodynamic couplings which allow radial assembly/disassembly provide all proven power transmission features you can expect from such solutions – but in addition, they greatly contribute to reduce the MTTR of drive systems of your bulk material handling equipment, increasing both, the productivity and profitability of industrial plants.
Comment