Case Study: Application of HENFEL bearing housings in iron ore pellet roller screens
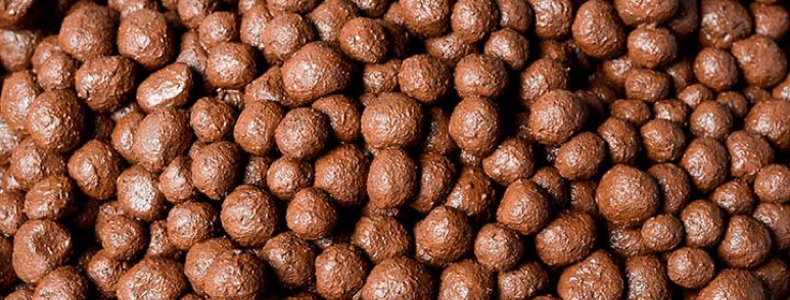
Before we dive into the case study, a little background information may be necessary. An iron ore pellet is a tiny iron ore ball (between 8 and 18mm of diameter) composed of pellet feed and iron ore fines, which are the finest forms of the iron ore, mixed with a flux (in Brazil usually limestone) and a thickener, which gives the pellets their consistency.
The Application
Unlike lump iron, when iron ore is in the form of pellet feed and iron ore fines, it cannot be fed directly into the blast furnaces used in the steel industry. Therefore, it undergoes a process called pelletizing.
The pellets are the most common base material of the steel industry; suffice to say their contribution is huge. We would have no cars, bridges, buildings, planes, bicycles or even household appliances without the iron and steel that derives from their production.
This case study’s goal is to present HENFEL’s solution for increasing the reliability of the pellet screens in three plants of an important customer in the Southeast region of Brazil.
The situation
Near the end of 2006, HENFEL's technical team was invited to assess the situation of the iron ore pellet screens installed in three pelletizing plants. The customer was facing an excess of non-scheduled maintenance shutdowns due to the premature contamination of the bearing housings that had been installed at that time.
Iron ore pellet roller screen
Upon investigation, the technical team was informed that between the years 2005 and 2006, 65 maintenance interventions had been necessary in order to solve problems, mainly due to premature bearing failures.
The solution
Based on the information gathered during the visit, HENFEL's engineering department developed a new model of bearing housing with a special seal, which is more suitable for the abrasive / aggressive work environment due to the presence of taconite powder.
Additionally, the team made recommendations to help solve other problems not directly related to bearing housings, such as the positioning of the gearboxes, the connection coupling, and the type of lubricant that was being used for the bearings.
The result
After the replacement of the problematic bearing housings, the MTBF (mean time between failures) of the bearings increased, and furthermore, throughout 2007 and 2008, there was an impressive reduction in the amount of necessary maintenance interventions.
Altogether, the maintenance operations of the roller screens lasted 4 hours and 33 minutes in 2007 / 2008. In comparison to 2005 and 2006, the downtime of the same equipment amounted to over 69 hours.
Overall, the solution reduced the amount of interventions (- 48 required) and increased the equipment availability by 65 hours.
Comment