All Couplings are not Equal: Smart Engineering Considers Both Technical and Economic Requirements
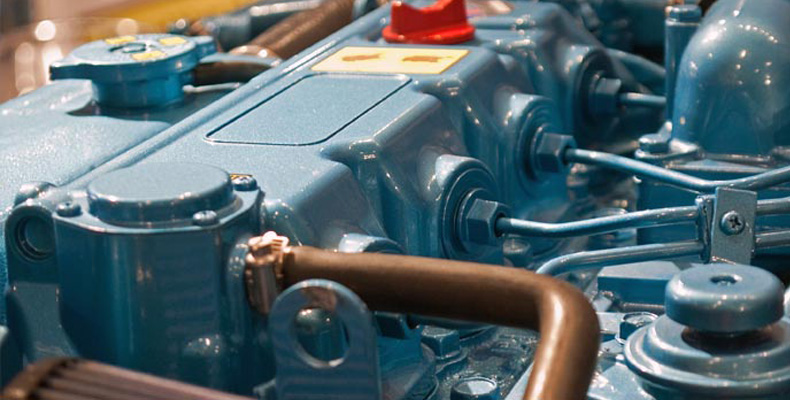
Bending stress, torque shock, natural frequency and resonance: all the machinery elements in drive systems – i.e. above all axes, shafts, bearings and couplings – must withstand such strains. The coupling plays a prominent system-influencing role which it continues to fulfill better and better due to advanced development.
A coupling normally connects two shaft ends: one coupling half on the side of the driving element, the input, and the other coupling half on the side of the driven element, the output. The coupling transmits the power of the driving machine between the two shafts, i.e. the rotary motion – the torque.
When selecting a coupling, the engineer has two basic questions in mind:
- What are the coupling's functions?
- Which system requirements does it have to satisfy?
The function is the determining factor for the coupling type. Couplings are classified as shiftable and non-shiftable couplings. Shiftable couplings comprise those types which can only be shifted at a standstill and those which can be engaged and disengaged during operation. Depending on the design, this is done by positive or frictional engagement. Non-shiftable couplings are subdivided into rigid, elastic and torsionally flexible couplings. The flexible couplings are again classified as universal joints and elastic couplings.*
In addition, the particular requirements of the application need to be considered, these are technical characteristics such as the weight of the coupling, its mass moments of inertia and the avoidance of vibrations caused by unbalance. Economic requirements also have to be taken into account, for instance, time and work effort for the installation, maintenance intensity and cost for replacement.
Rigid couplings: they transmit power, but torque peaks as well
Rigid couplings, for example disc couplings, do not compensate for misalignments and they transmit torsional vibrations undamped. They are best suited for precisely positioned shafts. Rigid couplings are often found where shaft sections are connected to long shaft lines, such as in transmission drives. Because no relative movement takes place in these couplings, they are resistant to wear. However, the stiffness of these couplings can only be varied to a lesser extent, with almost no adjustability.
In order to compensate for unavoidable shaft misalignments, universal joints are used. They are capable of compensating axial, parallel and angular misalignments. However, they are torsionally stiff and transmit torque shock loads in an undamped manner. Common types of these positive torque transmission couplings are gear couplings, steel disc couplings, universal joint or cardan joint couplings.
Flexible couplings: Power transmission with damping and compensation for misalignments
In addition to transmitting the torque between the drive and driven machine, flexible couplings, such as jaw couplings, have the function to compensate for angular, parallel and axial shaft misalignments within defined ranges. When the requirements are more complex, more attention is needed for the selection of the coupling. Shear pin and jaw couplings are able to compensate for axial misalignments and angular and parallel offset. They belong in the semi-flexible coupling category and are mainly used in drive lines with electric motors that have relatively uniform torque curves.
Drive systems with combustion engines feature non-uniform torque behavior with dynamically overlapping amplitudes. Torsionally flexible, and in particular highly flexible couplings, are able to dampen torsional vibration amplitudes and peak torques. By deliberately selecting and adapting the torsional stiffing of the coupling, the natural frequency of the driving equipment can be influenced and unavoidable resonances be moved into non-critical ranges. Therefore, when designing a torsional flexible coupling, the focus is put on both the stiffness and the damping property. One application example is the combined power and heat unit, where a torsionally flexible coupling connects a gas engine with a synchronous generator to produce electricity.
Increasing technical requirements on the coupling may also involve increasing costs because, common highly flexible couplings are expensive, and their maintenance and the replacement of the elastomer elements can employ much time and efforts. The new generations of couplings account for both requirement dimensions. Elastomer buffers arranged in series allow for the individual adjustment of the stiffness as well as for easy replacement of the buffers while the coupling is still mounted in place. This will not only reduce costs but time spent on maintenance as well.
* Main source: Professor Dr.-Ing. Horst Haberhauer, Ferdinand Bodenstein † (2005): Elemente der drehenden Bewegung. Springer Heidelberg.
Comment