Emergency Buffers for Ship Loaders: Thoughtful Design for Increased Safety and Efficiency
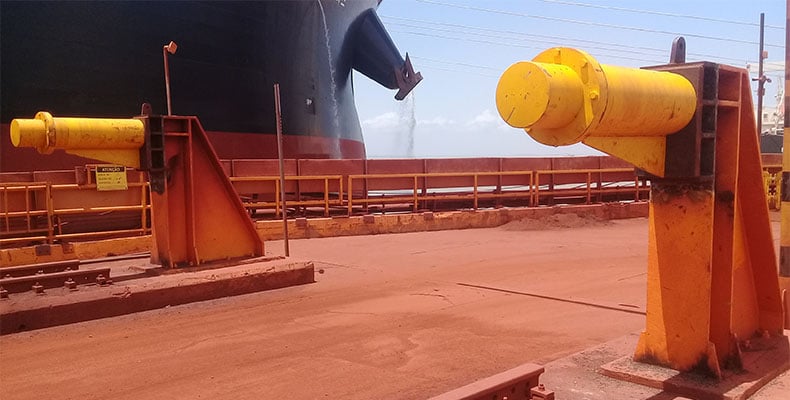
How RINGFEDER POWER TRANSMISSION implements a safe and maintenance-free end stop for a ship loader in Northern Brazil.
In a large mine in Northern Brazil, the journey of iron ore begins: the processed raw material is tipped from railway wagons onto a conveyor belt, which then transports it to a ship loader that moves along the dock on rails, loading the material into the cargo holds of ships up to 360 meters long. But what happens if the brakes of the ship loader fail? The secure answer is that emergency buffers are used as end stops to prevent major damages.
Previous emergency buffers were maintenance-intensive
The previously used hydraulic emergency buffers proved to be particularly maintenance-intensive and potentially environmentally harmful - primarily when hydraulic fluid leakage occurred. Therefore, a more sustainable and maintenance-free solution was needed.
The requirements were high: in the event of an emergency, the new buffer should be able to absorb an energy of 300,000 joules, divided into two buffers, while maintaining the existing connection dimensions.
Each of the two buffers consists of a parallel combination of the three friction spring sizes 24201, 19600, and 14000. To provide extra protection for unforeseen cases, each individual buffer was designed to absorb an energy of 189,000 joules with a preload force of 277 kN, a maximum spring force of 1850 kN, and a total spring deflection of 178 mm.
The spring deflection for the intended load case of 150,000 joules is 159 mm, resulting in a buffer utilization of approximately 90%.
Sustainable and maintenance-free RINGFEDER solution
The solution implemented by RINGFEDER involves the use of several friction springs that are nearly the same length as the original buffer. The new maintenance-free emergency buffers allow for retaining the existing connection dimensions while meeting the requirements for performance and environmental compatibility.
The solution impressively demonstrates how technological progress and thoughtful design can enhance safety and efficiency in the iron ore industry.
Comment