Safe Energy Absorption – DEFORM plus® Shock Absorbing Units
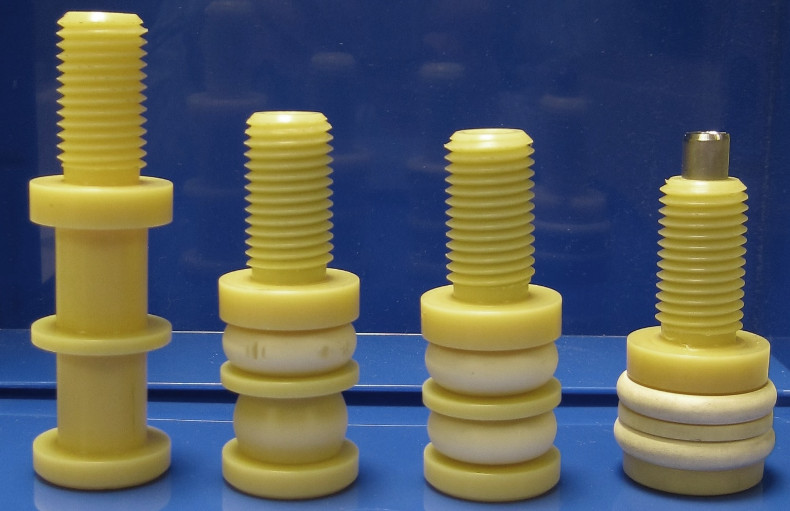
In our last blog article we compared the most commonly used damping systems in terms of their damping properties and highlighted the importance of installing such systems to protect your machines and components. Our comparison referred to dampers made of optimized synthetic polymers. In this article, we would like to present our shock absorbing units DEFORM plus®.
Why should a damping system be used?
As already explained, a moving mass can cause substantial damage upon impact, for example, in the event of a brake failure or operating error. In such critical situations, damping systems protect against great serious losses, because they transform motion energy into heat energy (friction during braking), or elastic potential energy (deformation of the damper).
DEFORM plus® Shock absorbing units
DEFORM plus® is a component which is tailored to the application and converts motion energy into deformation energy. This shock absorbing unit is mounted between a moving mass and an end stop, either by simply bolting it on or by inserting it in between the components located in the power flux. Since DEFORM plus® shock absorbing units can only be used once, they have to be replaced after each impact or crash.
If correctly designed, these shock absorbing units are able to reliably bring a moving mass to a stop while full function of the adjacent components is maintained. The shock absorbing units come in two type series:
Type 1
This model is one complete unit made of plastic with the inside guide made of steel. It needs a longer mounting depth than type 2, because it is equipped with a longer screw-in thread which takes in the steel guide upon deformation. Only the deforming elements are supported by the impact absorbing wall.
Type 2
In this design, only the actual deformation elements are made from plastic and the guide and fasteners are made from steel. These units are equipped with a thrust piece which is also made of steel, and are fastened to the receptacle by an internal screw. For this reason, the mounting depth is less than for type 1. On account of the thrust piece, however, you will need more space between the components located in the power flux. The actual deformation elements are also available individually and just need to be attached to the internal screw.
Function principle
The energy absorbing elements are tubular sections with a specifically calculated geometry. In the case of an axial load, they are not only compressed, but subjected to a bending load, with the fibers being stretched in circumferential direction:
After half of the nominal deformation travel, the stretch rate reduces relative to the axial deformation travel, so that the required force for deformation will not go further up. In contrast to other mechanical deformation elements, that have a progressively increasing force curve, the force of the impact is limited here. Only when the two surfaces of the discus-shaped pipe section contact each other again, the force continues to increase in accordance with the compression elasticity of the plastic (synthetic polymer) material.
Typical applications
You have seen DEFORM plus® shock absorbing units without knowing it – they are used e.g. for funiculars (emergency buffer stops in the stations), or in bumpers of streetcars to protect various components upon crashing into an obstacle.
Other typical applications can be found in the field of mechanical engineering, e.g. plants with linear gantries where DEFORM plus® units serve as an impact protection in the end positions.
They are also used in machining centers to protect different tools in all axes of rotation, or for rotary tables with fast oscillating movements where they serve as rotation limiter during over-swinging in the end positions.
Standard and custom designs
DEFORM plus® shock absorbing units are available with a nominal energy absorption from 30 J and a nominal force of 4 kN. For ambient temperatures which are permanently above 50°C, we offer a metal version of DEFORM plus® – these models are customized to the respective application.
The latest generation of DEFORM plus® units can also be used in explosion-proof rooms. Due to the encapsulation at the face, the impact from metal to metal is avoided.
Conclusion
In the event of a crash, DEFORM plus® shock absorbing units reliably protect valuable vehicles and machinery components against damage without requiring complex constructive measures. They also fulfill all guidelines to protect the environment.
Our shock absorbing units are available in many different standard models, or can be designed according to your specific requirements (depending on the quantity of required units). For this, our Engineering team only needs the dimensions of the available mounting space, the impact velocity, the ambient temperature and the involved masses. Please feel free to contact us if you require further information or have any questions regarding damping technology.
Comment