Mechanische Verfahren zur Oberflächenbehandlung von Bauteilen
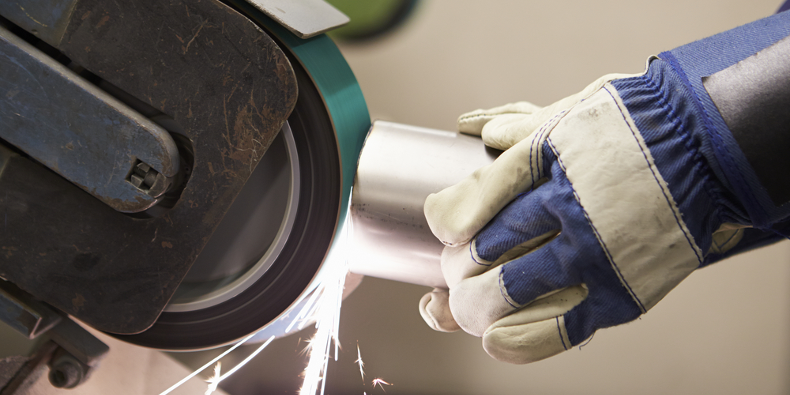
Die Ausführung von Bauteiloberflächen im Maschinenbau wie auch der Oberflächen von Produkten geschieht heutzutage nicht nur unter Designgesichtspunkten, sondern wird überwiegend auch durch technische Aspekte bestimmt. Und dabei hat bereits die Festlegung der Anforderungen an Bauteiloberflächen, wie z.B. bei einer Wellenkupplung, oftmals weitreichende Konsequenzen für den weiteren Produktentstehungsprozess, die entstehenden Kosten sowie letztlich ebenso auf den späteren Erfolg des Endproduktes.
Bestimmung der Oberflächenanforderungen
Schon durch die Bestimmung der Oberflächenanforderungen legen Sie im Vorfeld meistens auch die Auswahl an Werkstoffen und Fertigungsverfahren fest: So bedingen geforderte Eigenschaften von Bauteiloberflächen nicht nur bestimmte spätere Produktionsabläufe, sondern auch die Bauteilauslegung und –geometrie, die Produktfunktionalität, wie auch die haptischen Eigenschaften (mit Blick auf die Wertigkeit des Produktes) sowie das Erscheinungsbild.
In nahezu allen Praxisfällen stellen die Oberflächen die am meisten beanspruchten Bauteilbereiche dar. In der Regel sind ca. 85 % aller Schadensfälle auf nicht an den Einsatzfall angepasste physikalische Eigenschaften in Verbindung mit den hohen Beanspruchungen dieser Bauteilrandzone zurückzuführen. Denn ein Bauteil steht über die Oberfläche in Wechselwirkung mit seiner Umgebung.
Durch gezielte Beeinflussung der chemischen Zusammensetzung und der Mikrostruktur (überwiegend abhängig von der Werkstoffwahl sowie dem Fertigungsprozess) können bestimmte benötigte Eigenschaften der Bauteiloberfläche eingestellt werden, wie zum Beispiel:
- Härte,
- Festigkeit,
- Zähigkeit,
- Duktilität (Eigenschaft eines Werkstoffs, sich unter Belastung plastisch zu verformen, bevor er versagt),
- Dauerfestigkeit,
- chemische Resistenz,
- thermische- und elektrische Leitfähigkeit.
Rauheit und Glanz werden wiederum durch die Feingestalt (Bauteilgestalt in Verbindung mit dem Fertigungsprozess) bestimmt.
Bedeutung für die Beurteilung einer Oberfläche
Um Oberflächen genauer zu spezifizieren existieren mehrere unterschiedliche Oberflächenkennwerte. In der Praxis werden jedoch normalerweise nur zwei unterschiedliche Standardkennwerte mit Zahlen-werten beschrieben:
- Der Mittenrauwert "Ra"
- oder die gemittelte Rautiefe "Rz".
Das Problem ist hier, dass diese beiden etablierten Standardkennwerte oft nur eine stark beschränkte Aussagekraft über die Funktionalität der Oberfläche haben.
So kann der Mittenrauwert "Ra" z.B. nicht zwischen Spitzen und Riefen unterscheiden und so keine verschiedenen Profilformen erkennen. Da er auf einer starken Mittelwertbildung beruht, streuen die Werte nur gering und sind gut reproduzierbar. Die gemittelte Rautiefe "Rz" reagiert dagegen empfindlicher auf die Veränderung von Oberflächenstrukturen als "Ra".
Bei a) sind die Gleiteigenschaften und die Schmierstoffaufnahme gut, b) neigt zu abrassivem Verschleiß
Im Folgenden möchten wir Ihnen hier nun die Einteilung der Oberflächentechnik in ihre Hauptgruppen Oberflächenbehandlung und -beschichtung sowie die am häufigsten verwendeten Oberflächen-behandlungsverfahren erklären.
Mechanische Oberflächenbehandlung
Eine mechanische Oberflächenbehandlung erfolgt in der Regel mit den folgenden drei Zielsetzungen:
1. Veränderung der Oberflächenrauheit
Hierbei haben Sie zwei Optionen. Entweder Sie Polieren die Fläche, um sie feiner zu machen, oder Sie rauen sie an, um die Haftung zu verbessern.
2. Reinigen und Entfetten der Oberfläche
Um sicherzustellen, dass sich keine Fremdstoffe darauf befinden, wie Rost oder Zunder; oder natürlich, um alte Beschichtungen zu entfernen.
3. Verdichten der Oberfläche
Bei diesem Verfahren ist es Ihr Ziel gleichmäßigere Strukturen zu erzeugen oder eine Maßhaltigkeit zu erreichen.
Polieren – Feinbearbeitungsverfahren
Das Polieren ist ein glättendes Feinbearbeitungsverfahren für verschiedene Materialien. Die glättende Wirkung erreichen Sie in der Regel mit zwei Mechanismen:
Zum einen werden Rauhigkeitsspitzen der Oberflächenstruktur plastisch und teilplastisch auf diese Art geebnet (auch Presspolieren; engl. Burnishing). Zum anderen erfolgt je nach Art der Politur ein kleinster bis kleiner Werkstoffabtrag (Glanzschleifen), sowie auch ein Verfüllen von Vertiefungen. Die damit erreichte Oberfläche ist aufgrund der Glätte oft glänzend. Metall bearbeiten Sie meist maschinell mit rotierenden Polierscheiben aus Stoff, Filz oder Leder.
Das eigentliche Poliermittel tragen Sie entweder als Suspension oder als sogenannte Festpaste auf die Scheiben, die sogenannten Poliermittelträger, auf. Das Poliermittel besteht aus verschiedenen Fetten, Ölen und dem eigentlichen Poliermittel. Dies kann z. B. Tonerde, Aluminiumoxid, Chromtrioxid oder Ähnliches sein.
Schleifen
Beim Schleifen erfolgt ein Werkstoffabtrag durch harte Kristalle infolge reibender Relativbewegung zwischen Werkstück und Schleifmittel. Schleifen ist ein spanendes, wegbestimmtes Fertigungsverfahren zur Bearbeitung von Oberflächen oder zum Trennen von Werkstoffteilen mit Schleifmitteln und gebundenem Schneidkorn. Dies kann manuell oder auf Schleifmaschinen erfolgen.
Nach DIN 8580 gehört es zur Hauptgruppe Trennen. Außerdem gehört es zur Gruppe der Zerspanungsarten mit geometrisch unbestimmter Schneide. Auf das Thema Gleitschleifen werden wir in einem späteren Blogartikel näher eingehen.
Strahlen
Hierbei handelt es sich um eine Oberflächenbearbeitung, bei der Sie ein Strahlmittel mit sehr hoher Geschwindigkeit (bis zu 160 m/s ≙ 576 km/h) auf die Werkstücke lenken. Als Trägerenergie haben Sie Druckluft, Druckflüssigkeiten, Elektrostatik, Elektromagnetismus oder Schleuderräder zur Auswahl. Das Strahlergebnis hängt neben verschiedener Maschinentypen und Einstellungsparameter im Wesentlichen von der Art des ausgewählten Strahlmittels ab.
Durch die Strahltechnik können folgende Bearbeitungsziele erreicht werden:
- Entzundern / Entrosten,
- Entlacken / Entschichten (engl. Stripping),
- Entkernen / Entsanden (siehe Sandformverfahren),
- Reinigen,
- Oberflächenverfestigung (Kugelstrahlen, engl. Shot-Peening),
- Spanen / Entgraten (Kugelstrahlen, Sandstrahlen),
- Lackieren / Konservieren,
- Mattieren / Oberflächenfinish,
- Aufrauen.
Shot-Peening
Dieses Verfahren wurde unabhängig voneinander Ende 1920 bzw. Anfang 1930 gleichzeitig in Deutschland und den USA erfunden: Es beruht darauf, die Oberfläche eines Werkstückes mit einem "Kugelhammer" zu bearbeiten um die Druckeigenspannung zur Stabilisierung und Erhöhung der Lebensdauer zu induzieren.
Antriebselemente werden oft dem Shot-Peening-Verfahren unterzogen, um Druckspannung zu induzieren, wodurch das Risiko von Ermüdungsanrissen während des Betriebs beträchtlich reduziert wird.
Bei einer genauen Einhaltung aller Strahlparameter wie:
- Auftreffwinkel,
- Strahlzeit und Strahldruck (Druckluftstrahlen),
- Abwurfgeschwindigkeit des Strahlmittels,
- Typ des Strahlmittels und
- Flächenüberdeckungsgrad
können Sie die Lebensdauer vieler Werkstücke wie unter anderem Getriebeteile, Antriebs- und Kurbelwellen, Federn, Turbinenschaufeln bzw. auch generell von Turbinenelementen erhöhen. Die Überwachung des Strahlmitteldurchflusses erfolgt magnetisch oder durch Wiegeeinrichtungen, je nachdem ob ein metallisches oder nicht metallisches Strahlmittel zum Einsatz kommt. Ein wichtiger Punkt beim Shot-Peening oder "Verdichtungsstrahlen" ist die Strahlmittelwiederaufbereitung, die das Strahlmittel nach Form und Größe sortiert.
Mehr zu den gängigsten chemischen Oberflächenbehandlungsverfahren, die auch im Maschinenbau Anwendung finden, erfahren Sie in Teil 2 unserer Reihe zu diesem Thema. Abonnieren Sie unseren Blog, um nichts zu verpassen!
Kommentieren