Basics of Coupling Selection: The Safety Factor
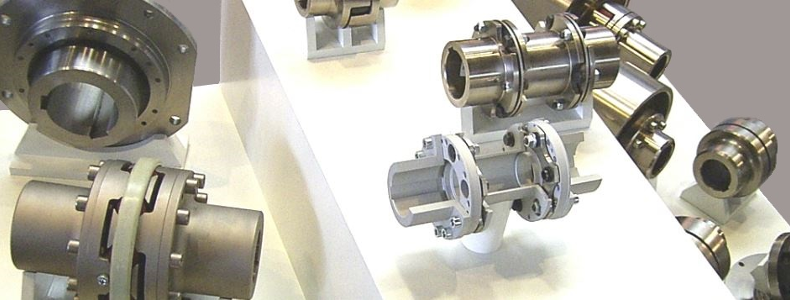
Engineers need to consider several aspects for selecting the appropriate coupling such as the type of installation, primary and secondary connection, available space of installation, ease of mounting and dismounting as well as maximum rotational speed and resilience of the coupling. To compensate physical parameters or changes that are not obvious the safety factor, also known as safety multiple or safety coefficient, is taken into account.
The safety factor indicates by which factor the failure limit of a component or material will be chosen. The failure limit will be set higher compared to the value of the theoretical determination based on static or dynamic calculations.
Safety factor 1 means that there are no safety margins in case of a failure. Failure mechanisms are mainly breakage or fatigue fractures (loss of fatigue strength). The idea of choosing a safety factor is to consider unknown tolerances in material, manufacturing, load assumption or other factors to prevent components from malfunctions. Possibly occurring impacts include critical environmental impacts, shocks at reversing operations, dynamic additional load due to unfavorable mass ratios, alternating torques and vibrations.
Depending on the safety significance the factor is between 1,1 and 2,1 in most cases. For extremely critical and safety-relevant parts, such as elevator ropes, it might be up to 10. In many cases engineers tend to very conservative estimations in defining loads and stresses which additionally increases the given safety.
Make the right choice
For a detailed dynamic examination engineers can select the coupling size based on a torsional vibrations analysis. With the program specific operating conditions can be simulated, such as start-up procedures or blocking situations. But in most cases the selection is based on estimated dimensioning of engine torque, depending on the uniformity of torque absorption with a general safety factor of Ss = 1,4 - 1,6. The following applies:
- Safety factor Ss = 1,4 for small coefficients of cyclic variation, for example multi-cylinder diesel engine generator drives
- Safety factor Ss = 1,6 for bigger coefficients of cyclic variation, for example diesel engine compressor drives
In addition to that the engineer has to consider another aspect: the generation of heat. The heat generated during the operating process emits via the surface of the aggregate, in most cases it affects adjacent areas, therefore the coupling as well. This is why the engineer needs to consider the material of the coupling. By choosing a flexible coupling the temperature coefficient Sθ needs to be taken into account. This factor describes the decrease of strength of elastomeric elements in case of increasing temperature.
Today couplings are considered to be optimized to the maximum with regard to functionality. Still for selecting a coupling the best possible option for each application counts since there are substantial differences when it comes to longevity of a coupling.
Comment