Chemical Processes for the Surface Treatment of Components (1)
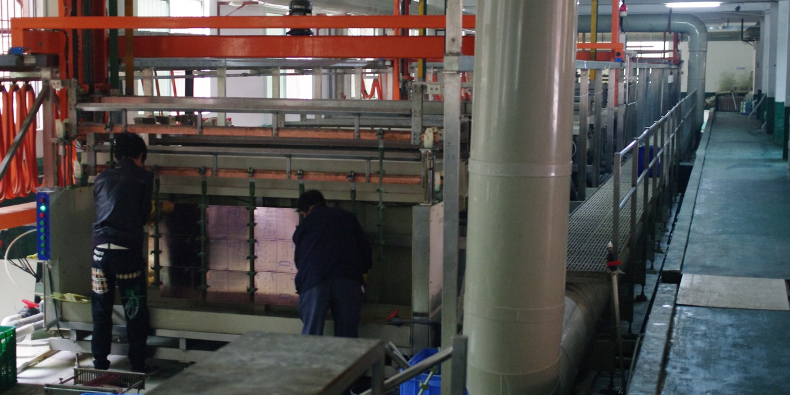
In our first blog article we presented the most common mechanical processes for the treatment of component surfaces. In this second part, we address the most frequently used methods of chemical surface treatments. The decision as to which of the following treatments should be applied is predominantly influenced by design points of view, technical aspects and the intended appearance of the product.
Chemical Surface Treatment
The common feature of all chemical treatments is that the chemical conversion layers are extremely thin. The thicknesses of layers typically range from 0.01 to 1.25 µm. For this reason, these layers are not suitable for outdoor corrosion protection unless post treatments are carried out. However, they provide a good undercoat for paints, aluminum and zinc coatings.
Chromate Conversion Coating
Chromate conversion coating encompasses a set of surface technology processes: In all of these methods, complex chromium compounds are formed on metallic surfaces due to the action of chromic acid. The chemical attack facilitates the dissolution of some surface metal, and the precipitated metal ions of the substrate are incorporated into the chromate layer.
The main purpose of chromate conversion coatings is corrosion protection. They are also applied to create an excellent retention of subsequent coatings, e.g. as a tarnish protection to reduce the visibility of fingerprints, or to provide a decorative finish (luster, color). Chromate conversion coating can be applied to aluminum, magnesium, silver, cadmium and zinc.
Phosphating
Phosphating is a process in which metal parts are immersed in an acid bath in order to create a thin, finely crystalline and water-insoluble phosphate on their surfaces. The light to dark grey metal phosphate layers are firmly anchored in the surface.
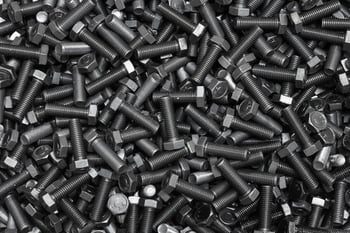
On account of the porous nature of the phosphate layer, it ensures optimum absorption of oils, waxes, color pigments and paints. For this reason, phosphate coatings provide optimum corrosion protection, and have also been proven over many years to serve as a stable base for subsequent coatings or painting operations.
Another property of the phosphate layer is that it reduces friction forces. This property is, for instance, utilized during the cold working of steel: in addition to improving the surface finish of the work piece, the service life of the tools is extended and the processing speed substantially increased. Furthermore, the high electrical resistance of phosphate coatings can be used for the electrical insulation of components.
Galvanizing
Galvanizing is a process by which a thin layer of zinc (about 80 to 150 µm) is deposited on steel surfaces, with the primary objective of protecting the metallic component against corrosion. The most commonly used galvanizing processes are:
- Hot dip galvanizing (hot dip metal coating),
- Sherardizing (thermal diffusion galvanizing),
- Electro-galvanizing,
- Mechanical galvanizing,
- Zinc flake coating.
Because of the great differences between the galvanizing techniques, the general term “galvanizing” is only descriptive to a limited extent. In a judgment dated March 12, 1969 (BGH, 12.03.1969 – I ZR 79/67), the German Federal Court of Justice clarified the meaning of this word. It said that, in general commerce, galvanizing refers to the application of a pure zinc layer. This would correspond with the general language use and would also be the concordant result of all galvanizing techniques, even though the execution of the galvanizing procedures differs in other respects.
In other words, what all galvanizing processes have in common is the application of a zinc coat. Coatings that, for example, are produced by zinc-rich paints do not belong to actual galvanizing processes.
Hot dip galvanizing
In the hot dip galvanizing process, a metallic coating is applied to steel by immersing the steel parts into a bath of molten zinc at a temperature of about 450°C. A distinction is made between two methods:
Batch galvanizing refers to a process where prefabricated articles (e.g. handrails) are individually hot dip galvanized, whereas in the steel strip process, semi-finished products (e.g. sheets) are galvanized on a continuous line.
These two methods differ with respect to the thickness of the zinc layer: In batch galvanizing, the thickness typically ranges from 50 to 150 µm, whereas the coating thickness in the steel strip process only lies between 5 to 40 µm. On account of the higher zinc coating thickness, the duration of protection for batch galvanized components is much longer – they generally reach a lifespan of more than 50 years.
Plating
Plating is a process in which two or more different metals are bonded in such a manner that further processing operations will not cause their separation. The objective of plating is either to let the work piece appear to be of a better material (e.g. by coating it with a higher quality metal) or to provide for higher resistance against environmental influences than the substrate metal would be able to endure. This inseparable bond is achieved with temperature and pressure.
Plating offers you many benefits: improvement of corrosion protection, higher surface hardness, better sliding properties and an enhanced aesthetic look. Commonly used bonds are, among others, nickel on steel, copper on steel as well as silver or gold on brass (also referred to as rolled gold).
Some of the typically employed methods are:
- Cladding of thin metal foils – i.e. bonding of at least two metallic strips by rolling them under high pressure. Normally, the metals are heated for this purpose.
- Pouring a liquefied metal onto another metal with subsequent rolling.
- Creating a thin layer of one metal on a plate of a second metal, then pressing together the metal plates to be joined. This thin coating can either be applied chemically, i.e. by using electroplating techniques, or mechanically, e.g. by pressure.
Black Oxide
With this process – which is covered by the DIN Standard 50938:2016-10 in Germany -, a very thin protective layer is formed on the surface of ferrous metals. It primarily serves the purpose of preventing corrosion. Black oxide is a chemical conversion coating and used in instances where a coating is required with no “build-up” of material.
By immersing the work pieces into an acid or alkaline solution, black iron oxide is formed on the surface. Due to the very thin thickness of this conversion coating of around 1 µm, the dimensional characteristics of the treated components remain virtually unaffected. Because of the porosity of the burnish coating, black oxide alone offers only a very mild corrosion protection, but the corrosion protection properties can be considerably enhanced by supplementary post treatments with oil or wax.
Another excellent feature of black oxide is that it improves the adhesion properties of metals and therefore serves as a good base for additional surface treatments, such as painting. In addition to a high resistance to bending and wear, the black oxide coating is resistant to temperatures of up to 300°C approximately. This process is predominantly applied in the field of mechanical engineering and in the tool making industry.
Apart from its function as corrosion protection and an adhesion base, black oxide is also used to upgrade the optical appearance of objects, e.g. to achieve an “antique” finish for screws or brass furniture hardware.
In the next part of our series on the topic of surface treatments you will learn more about:
- Chrome-plating
- Cadmium-plating
- Anodizing
- Hard coating
What might also be interesting for you: the mechanical processes for the surface treatment of components
Comment