Friction Springs - Experts in the Field of Damping Technology
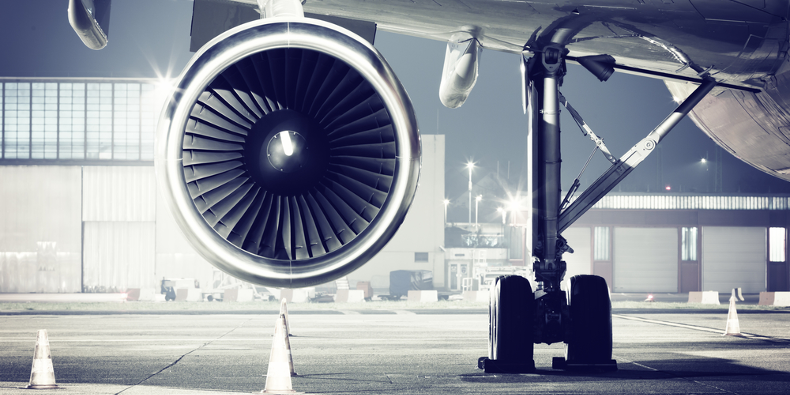
Friction springs are indispensible safety components in all fields of technology where suddenly occurring forces have to be taken up and kinetic energy absorbed, or where springs are required with relatively compact dimensions while also being able to sustain high forces. Expert friction springs are needed when it comes to the deceleration of moving masses in a quick, safe and precise manner.
Lars Jahnel, Application Engineer at RINGFEDER POWER TRANSMISSION explains:
„Friction springs are all-purpose elements and have a clear advantage over other damping systems. Of these advantages I want to mention just a few: For example, the springs perform high spring work though they are comprised of low weight (Fig. 1) and volume. The reason for this is that each individual volume element is uniformly utilized, because the circumferential stresses are equally distributed over the cross-sectional area of each individual volume element. This minimizes dimensions and weight, a considerable advantage for applications such as aerospace technology.
Fig. 1: Weight utilization η of various springs
Another advantage is their high damping capability, which is 66 % when using our standard grease, or 33 % to 66% when alternative greases are used (Fig. 2). The energy induced into the application is taken up quickly and resonance phenomena are suppressed entirely (Fig. 3).
Fig. 2: Damping and spring work
In addition, friction springs in block configuration are fail-safe. Their design as block springs ensures that permissible stresses are not exceeded so that both the friction spring and the equipment will not suffer any damage.
Fig. 3: Overload protection with block configuration
Friction springs are used wherever high kinetic energies have to be taken up and dampened, or where springs with relatively small dimensions are required for high forces. The range of application for friction springs is very versatile. Basically, they serve three areas which can also be combined with one another: overload protection, clearance compensation and energy absorption. Some application examples are shown below:
Challenges with drilling equipment
For highly demanding drilling equipment, the stress on the dampers is particularly great, but this does not produce a problem for friction springs. The increased compressed air requirements and the high damping are ideal for such applications. Furthermore, the increased reliability of friction springs by virtue of their design is a decisive advantage over other damping systems. In this case the friction spring does not only provide for energy absorption, but also compensates for clearances which may occur between the individual components during continuous operation.
Aerospace engineering
Friction springs are ideal elements for use in aerospace applications. Their low weight, the compact design and their independence from temperatures are essential prerequisites in these applications. Among other applications, friction springs are used in landing flaps or emergency exit doors on various types of airplanes.
Friction springs are also installed in the Mars Rover Curiosity where they prevent resonance phenomena and thus enable scooping of rock dust on Mars.
Use in Valves
At a speed of 1500 m/s a pellet of frozen hydrogen is shot through a valve into high vacuum. The closing speed of the valve is 25 m/s and is dampened by a coated friction spring.
Friction springs in furnaces
When heavy scrap parts drop from high heights, friction springs are required to protect the plant from damage. With a great number of draw gears and an energy absorption capacity of up to 80,000 Joule/piece, these parts are contained above the melt. In addition, high thermal loads have to be sustained on a continuing basis.
Shock absorbance in roller mills
In roller mills, the rolling stock on the roller tables has to be brought to a stop in certain points or at the end. On account of the relatively high speed and masses, pre-dampers with a high energy absorption capability are needed. Buffers equipped with friction springs provide for utmost operational safety in these harsh environments.
Lateral oscillations with antenna installations
Slender structures such as antenna installations can be excited to strong lateral oscillations due to wind. Such oscillations may jeopardize the entire building. This can be remediated by the use of oscillation dampers which together with an oscillatingly suspended mass, reliably protect smoke stacks and antennas in all temperature conditions. Hence, they act in pull and push direction (Fig. 4).
Fig. 4: Force-stroke diagram from an oscillation damper
Protection of gasometers
If not only high speeds, but high masses and very low stress speeds are also involved, friction springs lend themselves as effective solutions. In gasometers, buffers are used to avoid cracks in the shell. Our buffers stand out for their long operating life.
Prevention of damage to crushers and mills
From time to time material gets into crushers and mills that cannot be crushed or pulverized. In order to prevent damage to the crusher or mill, friction springs are installed to serve as an overload protection. These springs are highly pre-tensioned to allow the crusher jaws or grinding cones to draw aside in the event of an overload. Friction springs are particularly suitable for this, because they need little installation space and prevent excessive rebounding on account of their damping capability.
Friction springs also play a decisive role in the field of earthquake protection. More details will follow in a separate article.. :)
Comment