How to Achieve Efficiency: Sustainable Maintenance Management Requires Cooperation
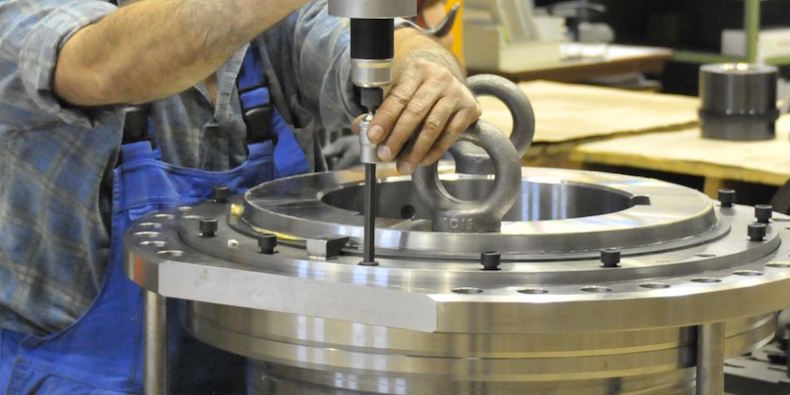
Designers of plants and machines strive for the optimal selection of a coupling for the complete system with many variables requiring consideration. In most cases, the main focus is not how maintenance-friendly the product is. Yet – one might say. For a sustainable improvement of the longevity and efficiency of plants, a stronger involvement of maintenance is a must.
Unforeseen machine break downs are the worst case for the maintenance technician or maintenance engineer. For plant operators they mean severe costs. Usually these break downs are caused by the system. Three examples:
- Order of components: Improperly sized or poor quality components do not only fail much earlier but might also lead to damage of the machine.
- Acceptance inspection of machines: If maintenance experts are involved, significant design faults can be detected much earlier and inspection and control measures can be adjusted according to the actual conditions of the components. But this rarely happens in practice.
- Utilization of machines: Process-oriented inspections and condition-based maintenance can avoid failures. The findings gained in this process help to optimize the plants in the long term, to increase quality and reliability and to save costs. Still it is quite rare that such key indicators are developed and checked.
Avoiding costs caused by a lack of sustainability
Both direct and indirect costs vary from company to company. Estimates range from 10 to 40 percent depending on industry and type of plant.
Maintenance directly impacts plant availability, repair costs and efficiency increasing the potential risks to business operations.
The responsible team members have to deal with the pressure created by the increasing strategic relevance of maintenance. Nevertheless, their practical experience is frequently not considered.
Paradigm shift: smart maintenance
There is a paradigm shift looming; concepts of smart maintenance are the driving forces. More and more companies are deciding to establish a dedicated department for maintenance management.
Until recently maintenance rarely played an important role in the strategic vision of a company. Nowadays there is, at least theoretically, a change with the implementation of specialized teams. Those who are serious about maintenance management define measures, targets and key indicators in cooperation with these departments. Good targets are thereby realistic, which means achievable, concrete and focused on long-term success. Short-term adjustments are defined by milestones or sub-targets.
The potential of maintenance management will be recognized if defined processes are implemented; experiences and evaluations are documented and analyzed as well as evaluated on a regular basis. Utilizing this heightened focus, for example, frequent break downs or an above-average lubricant consumption can be reported to manufacturers and suppliers. In addition a manufacturer is able to better define specific requirements when ordering new machines or components based on these evaluations.
Comment