What is the reason for using a coupling with limited end float?
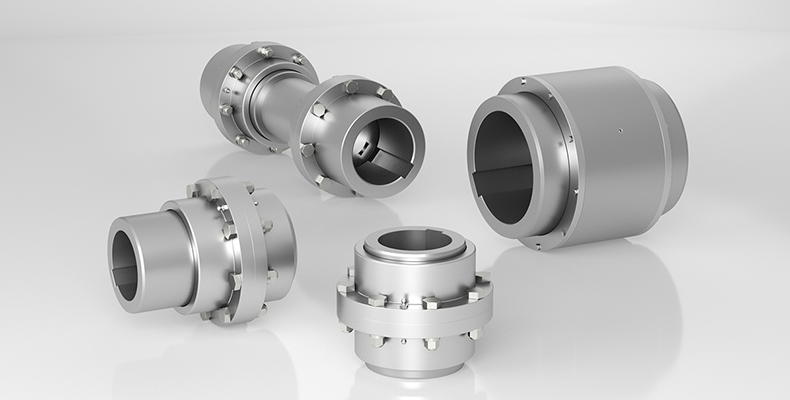
A coupling is an element of a drive line that primarily serves the purpose of transmitting power from one shaft to another, thereby providing for the connection of the driving and driven machine. At the same time, shaft misalignments, e.g. caused by assembly inaccuracies, should be compensated by the coupling while generating minimum reaction forces.
The distinction is made between angular, radial and axial shaft misalignments which may also occur simultaneously. Depending on the coupling type you choose, the dynamic behavior of the entire drive line, and consequently of the machine and its production process, can often be influenced by adjusting the torsional stiffness of the coupling.
Electric motors as a commonly used drive
Let us first have a look at the drive end: In most cases, electric motors are used here which convert electric energy into mechanical energy. An electric motor mainly consists of a stationary stator and a rotating rotor. The latter is composed of a shaft which is supported in the motor housing, and a coil that is wound on this shaft.
When applying voltage to the stator, the current flux generates a magnetic field which in turn generates a magnetic reaction of the coil in opposite direction to the magnetic force. With the shaft being supported in the direction of rotation, the rotor is free to turn - apart from a small mechanical resistance out of the bearing – and is set into rotation. The magnetic force produces a torque that acts on the shaft, and this torque is determined by the power and the resulting speed. The torque is taken up by the coupling and transmitted to the driven machine.
The rotor bearing
Fixed bearing/ floating bearing principle
Let us now look at the rotor: The reaction force resulting from its entire weight – i.e. the force resulting from both, the shaft and the coil – is transmitted via the shaft bearing to the motor housing and into the foundation. Anti-friction bearings are most commonly used to support the shaft. Only when high motor powers are involved, other bearings like sleeve bearings are often used. The selection of the bearing affects how the rotor is located in the axial direction. With roller bearings, the fixed bearing-floating bearing principle is preferably applied, i.e. the shaft is axially located at the fixed bearing in the housing.
Calculation software MDESIGN of the TEDATA GmbH, Bochum, Germany. More information under
Motor shafts supported by sleeve bearings
In contrast to this, a motor shaft supported on sleeve bearings is allowed more axial movement which is attributable to the structural design of the bearings. In the following, we only refer to electric motors that are equipped with sleeve bearings, but do not have an additional axial bearing.
In this configuration, rotors are able to move axially by several millimeters. The coil has been wound in such a way that, in the center of the motor, the sum of all generated magnetic forces exclusively acts in the direction of rotation, and thereby contributes to maximum torque build-up.
As the rotor has more freedom to move axially, the drive line must be aligned such that the rotor remains at its magnetic centre. The correct way to align the shaft is indicated by a mark provided between the shaft and the stationary motor housing.
Limited end float
For limiting the end float or end play, a fixed bearing of another shaft is required which will axially locate the rotor shaft. The fixed bearing is arranged on the opposite side of the drive – at the non-drive end: This may, for instance, be the bearing of a gear shaft in a gearbox or the shaft bearing of a powerful compressor.
As mentioned in the beginning, a standard coupling allows for the compensation of axial misalignment of two shafts. However, this feature of the coupling prevents a rotor shaft supported in sleeve bearings from being properly aligned to the specified values. It is, therefore, necessary to use a coupling with limited end float.
RINGFEDER® limited end float gear coupling
As this denomination suggests, a defined end float in the axial direction is provided for. The freedom of movement which helps compensate for angular and/or radial shaft misalignments is not constrained if a limited end float coupling is used.
To answer the initial question:
For motors with sleeve bearings you should always use limited end float couplings so that the magnetic center of the rotor can be aligned to a fixed bearing arranged opposite to the coupling, and that the rotor remains at its magnetic center during acceleration and deceleration of the driving machine. If this was not the case, undesirable magnetic forces would develop in the axial direction which can adversely affect the operating performance.
To learn more about our RINGFEDER® TNZ series couplings, visit our website or send us contact request.
Comment