Reciprocating Engines in Combined Heat and Power Units: Is Higher Power without Loss of Energy Efficiency Possible?
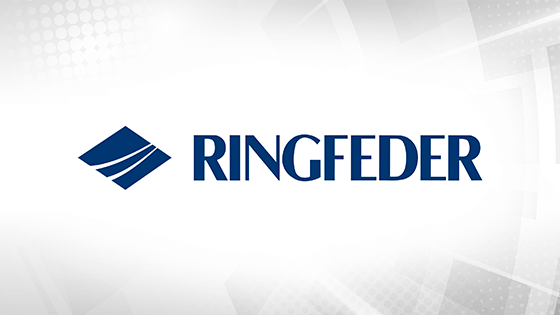
The combined heat and power technology (CHP), in particular co-generation units, have long been a part of the industrial energy transition. However, the large potential of combined heat and power units is still underutilized. The reason for this, among others, is because of the properties of the installed drive technology: for instance, the non-uniform torque of reciprocating engines. New components promise more power with consistently good energy efficiency.
The development of combined heat and power technology revolutionized the way energy is utilized because it combines the centuries-old technologies of generating electricity on one side and heat on the other side. This is virtually realized in combined heat and power units where slightly adapted diesel engines, gas or steam turbines are generally installed.
According to the Bundesverband KWK e.V. (German CHP Association) about 20 % of industrial energy is currently being self-produced. Depending on the required heat (space heating or process heat) as well as power consumption, various CPH technologies are suitable. CPH units are worthwhile and beneficial in almost all industries, from daylight mining to textile processing – and often used together with reciprocating engines.
The principle of combined power and heat units: Liquid or gaseous fuels drive an engine that in turn produces electricity through a generator. The waste heat is also used for space heating or process heat. Together with renewable energy sources, these combined power and heat units are regarded as a vital factor of the energy transition. Original source of image: Bundesverband KWK e.V.
Combustion engines provide high output – but also cause uneven operation
Combustion engines such as Otto or diesel engines have a total efficiency of up to 90 per cent, an electrical efficiency of about 46 per cent and an electrical power of about 20 megawatt in cogeneration plants. They supply space heating and process heat. However, reciprocating engines feature a non-uniform torque. This means that possible excitations from the engine disturb the smooth operation of the system. To avoid this, the engineer selects a highly flexible coupling. With this coupling he tunes the natural frequency away from the critical range.
Along with increasing requirements on the flexibility and efficiency of the drive, the demands on engineering and design inevitably increase as well. A higher torque is desired. However, this will often lead to an increase in non-uniform torsional movements, also in CHP units, and can, therefore, only be realized at the expense of efficiency losses. An optimal – and this means a soft characteristic curve is attained in co-generation plants by installing a coupling to the drive line that allows for an utmost torsion angle even at a high torque.
The beneficial effects of such a coupling installed in a CHP plant are shown below:
Effect of different elastomeric couplings on the operational smoothness of a CHP unit: The standard design (red) leads to strong vibrations; the TNR coupling with elastomer buffers arranged in series (green) provides for considerably smoother operation.
Comment