Chemische Verfahren zur Oberflächenbehandlung von Bauteilen (1)
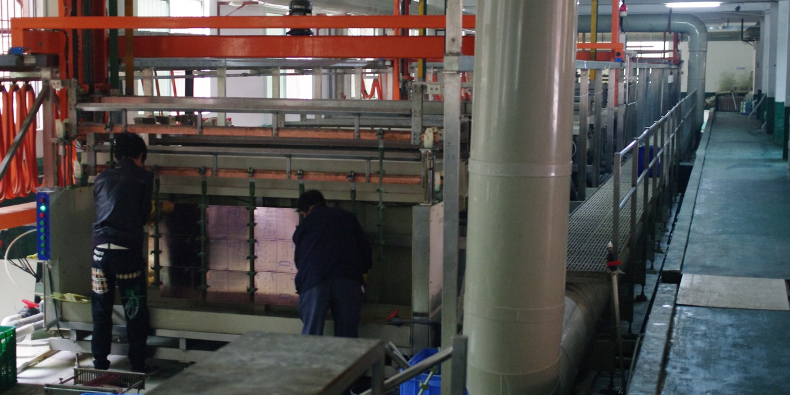
In unserem ersten Blogbeitrag haben wir Ihnen die gängigsten mechanischen Verfahren der Oberflächenbehandlung von Bauteilen vorgestellt. In unserem zweiten Teil möchten wir jetzt näher auf die am häufigsten angewendeten chemischen Verfahren der Oberflächenbehandlung eingehen. Die Entscheidung welches der folgenden Verfahren Sie für ein Bauteil einsetzen sollten, wird maßgeblich von Designgesichtspunkten, technischen Aspekten und dem festgelegten Erscheinungsbild des Produktes beeinflusst.
Chemische Oberflächenbehandlung
Bei der chemischen Oberflächenbehandlung sind die chemischen Umwandlungsschichten sehr dünn. Die Schichtdicken betragen hier in der Regel nur zwischen 0,01 und 1,25 µm. Aus diesem Grund sind diese Schichten im Freien als Korrosionsschutz ohne zusätzliche Verfahren nicht einsetzbar – sie sind jedoch ein guter Haftgrund für Lackierungen, Aluminium- und Zinkbeschichtungen.
Chromatieren
Das Chromatieren umfasst eine Gruppe von Verfahren der Oberflächentechnik: Bei allen werden auf metallischen Oberflächen durch die Einwirkung von Chromsäure komplexe Chromsäuresalze (Chromate) gebildet. Bei diesem Vorgang wird der Grundwerkstoff angelöst und die gelösten Metallionen des Grundwerkstoffs werden in die Chromatschicht "eingebaut".
Die häufigste Funktion von Chromatschichten ist der Korrosionsschutz. Sie werden aber auch zur Erzeugung eines Haftgrundes für nachfolgende Schichten eingesetzt, z.B. als Anlaufschutz (Silber), zur Verringerung der Sichtbarkeit von Fingerabdrücken oder zur Veränderung des Aussehens (Glanz, Farbe). Chromatierungsverfahren können Sie bei den Werkstoffen Aluminium, Magnesium, Silber, Cadmium und Zink anwenden.
Phosphatieren
Bei der Phosphatierung handelt es sich um einen Prozess, bei dem im Tauchverfahren auf Metalloberflächen dünne, feinkristalline und wasserunlösliche Phosphate erzeugt werden: Die hell bis dunkelgrau gefärbten Metallphosphatschichten sind in der Oberfläche des Metalls fest verankert und weisen zahlreiche Hohlräume und Kapillaren auf.
Durch diese erhalten die Schichten ein gleichermaßen optimales Aufsaugvermögen für Öle, Wachse, Farbpigmente und Lacke. Daher hat sich das Phosphatieren sowohl als Korrosionsschutz, wie auch als Haftgrund für Farb- und Lackanstriche seit vielen Jahren bewährt.
Eine weitere Eigenschaft der Phosphatschicht ist ihre Fähigkeit, Reibungskräfte herabzusetzen. Diese Eigenschaft wird unter anderem bei der Kaltumformung von Stahl ausgenutzt: Denn so lässt sich neben einer Verbesserung der Oberflächengüte des sogenannten "Ziehlings" bei verlängerten Standzeiten der Werkzeuge auch die Verarbeitungsgeschwindigkeit wesentlich erhöhen. Außerdem können Sie den hohen elektrischen Widerstand von Phosphatschichten zur elektrischen Isolierung von Bauteilen nutzen.
Verzinken
Beim Verzinken wird Stahl mit einer dünnen Schicht Zink (~80 bis 150 µm) versehen, um ihn primär vor Korrosion zu schützen. Die gängigsten Verzinkungsverfahren sind dabei:
- Feuerverzinken (Schmelztauchverzinkung),
- Sherardisieren (Diffusionsverzinkung),
- galvanische (elektrolytische) Verzinkung,
- mechanische Verzinkung
- Zinklamellen / Binder-Systeme
Wegen der großen Unterschiede zwischen den einzelnen Verfahren ist die pauschale Bezeichnung "Verzinken" also nur eingeschränkt aussagefähig. Hier hat der Bundesgerichtshof in seinem Urteil vom 12. März 1969 (BGH, 12.03.1969 - I ZR 79/67) klärend festgestellt:
„Der Verkehr verstehe unter einer Verzinkung, daß ein reiner Zinküberzug aufgebracht werde, denn das entspreche dem Sprachgebrauch und sei auch das übereinstimmende Ergebnis aller Verzinkungsverfahren, wenn diese auch in sonstigen Beziehungen abweichend verliefen.“
Die Gemeinsamkeit der Verzinkungsverfahren ist demnach das Aufbringen eines reinen Zinküberzuges. Beschichtungen, die z.B. durch Zinkstaubfarben erzeugt wurden, werden entsprechend nicht zum eigentlichen Verzinken gezählt.
Feuerverzinkung
Unter einer Feuerverzinkung versteht man das Überziehen von Stahl mit einem metallischen Überzug durch Eintauchen des Stahls in eine Schmelze aus flüssigem Zink, dessen Temperatur bei ca. 450 °C liegt. Hier unterscheidet man zwischen zwei Verfahren:
Beim Stückverzinken werden i.d.R. vorgefertigte Stahlteile (z.B. ein Geländer) verzinkt, während beim Bandverzinken (sog. "kontinuierliches Feuerverzinken") Halbzeuge (z.B. Bleche) in einem Endlos-verfahren verzinkt werden.
Dabei unterscheiden sich beide Verfahren aber auch mit Blick auf die Zinkschichtdicke: Diese liegt beim Stückverzinken in der Regel zwischen 50 und 150 µm, beim Bandverzinken hingegen bei nur 5 bis 40 µm. Aufgrund der größeren Zinkschichtdicke ist die Schutzdauer von stückverzinkten Bauteilen höher – sie erreichen i.d.R. eine Nutzungsdauer von mehr als 50 Jahren.
Plattieren
Beim Plattieren werden zwei oder mehrere verschiedenartige Metalle so miteinander verbunden, dass die Weiterverarbeitung ohne Gefahr einer Trennung erfolgen kann. Ziel des Plattierens ist, den Arbeitsgegenstand entweder als aus besserem Material bestehend erscheinen zu lassen (z.B. bei Aufbringen einer höherwertigen Metallschicht) oder eine größere Widerstandsfähigkeit gegen Umgebungseinflüsse zu geben, als sie das als Unterlage dienende Metall besitzt. Diese untrennbare Verbindung wird durch Temperatur und Druck erreicht.
Mit Plattieren können Sie einen Korrosionschutz, eine höhere Oberflächenhärte, bessere Gleiteigenschaften oder ein wertigeres Aussehen erzielen. Gängige Verbindungen sind u.a. Nickel auf Stahl, Kupfer auf Stahl sowie Silber oder Gold auf Messing (sog. Gold-Doublé) zu nennen.
Einige der hier üblicherweise verwendeten Techniken sind:
- Aufwalzen von dünnen Metallfolien – also das Zusammenpressen der miteinander zu plattierenden, i.d.R. erhitzten Metalle
- Aufgießen eines flüssig gemachten Metalls auf das andere Metall und darauffolgendes Auswalzen
- Erzeugung einer dünnen Schicht des einen Metalls auf einer Platte des anderen Metalls und darauffolgendes Zusammenpressen der zu vereinigenden Metallplatten. Diese dünne Schicht kann entweder auf chemischem Weg, d.h. mittels galvanotechnischer Verfahren (Elektroplattieren) oder auf mechanischem Weg (z.B. durch Aufreiben oder Aufpressen) aufgebracht werden.
Brünieren
Beim Brünieren – abgleitet von französisch "brunir" (bräunen) – wird eine schwache Schutzschicht auf eisenhaltigen Oberflächen gebildet. Das Verfahren ist in Deutschland in der DIN-Norm 50938:2016-10 festgelegt und dient in erster Linie dazu Korrosion zu vermindern; bei der der Brünierung handelt es sich nicht um eine Beschichtung.
Durch Eintauchen der Werkstücke in saure bzw. alkalische Lösungen bilden sich auf der Oberfläche schwarze Mischoxidschichten (Edelrost): Durch die geringe Dicke dieser sog. "Konversionsschicht" von etwa 1 µm bleiben die brünierten Werkstücke weitestgehend maßhaltig. Wegen der Porosität der Brünierschicht besitzen sie jedoch nur einen geringen Korrosionsschutz, der sich aber durch Beölen oder Befetten deutlich verbessern lässt.
Eine Brünierung dient auch als Haftgrund für weitere Oberflächenbehandlungen wie z.B. das Lackieren. Die Brünierschicht ist weitgehend biege- und abriebfest sowie bis etwa 300 °C temperaturbeständig. Dieses Verfahren wird in erster Linie im Maschinen- und Werkzeugbau eingesetzt.
Abgesehen von der Funktion als Korrosionsschutz und Haftgrund wird die Brünierung aber auch zur optischen Aufwertung von Gegenständen eingesetzt, z.B. um ein "antikes" Aussehen zu erreichen, wie bei Schrauben oder Möbelbeschlägen aus Messing.
Im nächsten Teil unserer Reihe zum Thema Oberflächenbehandlung erfahren Sie mehr über
- Verchromen
- Cadmieren
- Eloxieren
- Hartcoatieren
Das könnte Sie auch interessieren: die mechanischen Behandlungsverfahren für Oberflächen
Kommentieren