Chemische Verfahren zur Oberflächenbehandlung von Bauteilen (2)
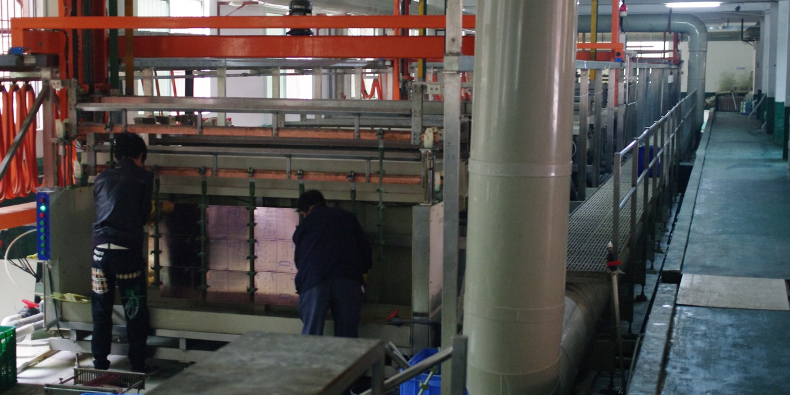
Teil 3 unserer Reihe zum Thema Oberflächenbehandlung von Bauteilen. Aufgrund der vielen Möglichkeiten an chemischen Verfahren haben wir diese aufgeteilt und in unserem letzten Artikel bereits die folgenden vorgestellt:
- Chromatieren
- Phosphatieren
- Verzinken
- Plattieren
- Brünieren.
Nun möchten wir Ihnen die noch nicht erwähnten üblichen chemischen Verfahren der Oberflächenbehandlung vorstellen.
Verchromen
Das Verchromen dient in erster Linie dem Korrosionsschutz und wird unterteilt in Glanzverchromung, Schwarzverchromung und Hartverchromung.
Glanzverchromung
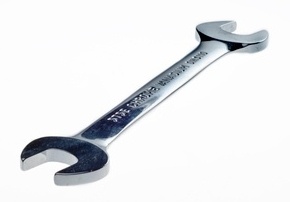
Bei diesem Verfahren, dem „dekorativen Verchromen", wird galvanisch eine sehr dünne Chromschicht von meistens 0,2 bis 0,5 µm aufgetragen.
Wegen der geringen Dicke solcher Chromschichten wird der Glanz des fertig verchromten Werkstücks nicht nur von der Chromschicht selbst, sondern auch von der darunterliegenden Schicht – in der Regel verwendet man hier Nickel – bestimmt.
Schwarzverchromung
Mittels spezieller Zusätze und einer höheren Stromdichte scheiden sich hier Chromschichten in einer tiefschwarzen Farbe ab. Die Schwarzchromschicht ist dabei eine der wenigen tiefschwarzen Oberflächen, die elektrisch leitend sind.
Da die Härte von Schwarzchromschichten aber nur bei ca. 250 bis 350 HV (Vickershärte resp. Vickers Hardness Number, VHN) liegt, sind sie nicht so kratz- und verschleissfest wie z.B. ein Glanzchromüberzug. Das können Sie jedoch etwas verbessern, indem Sie das Bauteil nach dem Beschichtungsprozess mit einem speziellen Öl behandelt. Auch die Schwarzverchromung wird für dekorative Zwecken genutzt.
Hartverchromen
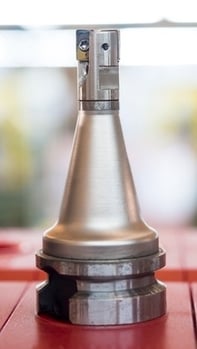
Die Bezeichnung "Hartverchromung" ist etwas irreführend da sie impliziert, eine Hartchromschicht sei härter als eine (dünnere) Glanzchromschicht. Tatsächlich ist die sie aber etwa gleich hart wie die dünnere Glanzchromschicht.
Eine normale Glanz- oder Hartchromschicht enthält ein dichtes Netz sehr feiner Risse die für das Auge nicht sichtbar sind und die Sie auch nicht ertasten können:
Diese „Rissigkeit“ von Chromschichten macht verständlich, dass eine Glanzchromschicht allein – trotz der ausgezeichneten Eigenschaften des Chroms – noch keinen guten Korrosionsschutz bewirkt. Ein zuverlässiger Korrosionsschutz entsteht daher erst in Verbindung mit geeigneten Zwischenschichten (i.d.R. Nickel oder Kupfer und Nickel). Diese Rissstruktur ist für manche Spezialfälle sogar vorteilhaft, da so z.B. ein Ölfilm besser haften kann.
Cadmieren
Unter Cadmieren versteht man das elektrogalvanische Aufbringen einer dünnen Schicht Cadmium auf Metalle, wodurch diese vor allem gegen Angriffe durch Alkalien geschützt werden. Der Widerstand von Cadmiumdeckschichten ist mit dem von Zinkschichten vergleichbar, sie können aber auch verchromt werden. Die Deckschichten finden beispielsweise bei Schraubenverbindungen Anwendung, weil sie letztendlich für ein konstantes Anziehmoment und gute Demontagemöglichkeiten sorgen.
Aus diesem Grund wird Cadmium auch in besonderen Fällen in der Luft- und Raumfahrt, Offshore, im Bergbau sowie im Kernenergiebereich eingesetzt. Es gibt allerdings auch andere Bereiche, in denen Cadmieren wegen seiner hohen Toxizität in Deutschland verboten ist, wie z.B. als Oberflächen-beschichtung von Schrauben oder als Farbzusatz. Für den größten Teil der Anwendungsgebiete von Cadmium wurden mittlerweile jedoch adäquate Alternativen gefunden, wie zum Beispiel "Zink gelb passiviert".
Eloxieren
Obwohl Aluminium ein sogenanntes „unedles Metall“ ist, reagiert es wegen seiner Passivierung bei Raumtemperatur nur oberflächlich mit Luft und Wasser: Um diesen Vorgang nicht dem Zufall zu überlassen, wird durch eine anotische Oxidation eine oxidische Schutzschicht auf das Aluminium aufgebracht. Dabei wird, im Gegensatz zu den galvanischen Beschichtungsverfahren, die Schutzschicht nicht auf dem Werkstück niedergeschlagen, sondern durch Umwandlung der obersten Metallschicht ein Oxid bzw. Hydroxid gebildet.
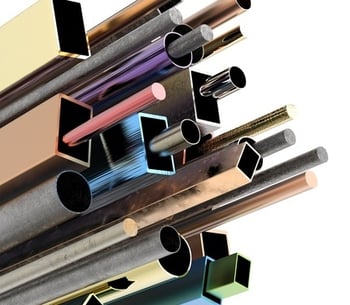
Auf diese Art entsteht eine 5 bis 25 µm dünne Schicht, die tiefere Schichten solange vor Korrosion schützt, wie keine Lücken (beispielsweise durch eine mechanische Beschädigung) darin entstehen. Die atmosphärische Oxidschicht des Aluminiums – die sich durch eine natürliche Oxidation ergibt – beträgt im Vergleich dazu lediglich wenige Nanometer.
Die Oxidschichten können nach dem Eloxieren eingefärbt werden, z.B. indem Sie sie in eine heiße Farbstofflösung tauchen (siehe Foto). Durch das Eloxieren lassen sich Härten zwischen 200 HV und 400 HV erreichen.
Hartcoatieren
Das Hartcoatieren bezeichnet man auch als „Harteloxieren“ oder „Hartanodieren“. Prinzipiell wird hier wie beim Eloxieren eine elektrolytische Oxidation von Aluminiumwerkstoffen in Gang gesetzt, um eine Schutzschicht zu erzeugen. Diese dient als Verschleiß- und Korrosionsschicht und weist in Abhängigkeit vom Gegenstück gute Gleitlaufeigenschaften auf, die durch eine PTFE-Imprägnierung noch verbessert werden kann.
Im Gegensatz zum Eloxieren, das bei Raumtemperatur und relativ geringer Stromstärke durchgeführt wird, arbeitet man beim Harteloxieren bzw. Hartanodisieren mit sehr hohen Stromstärken. Alle Aluminiumlegierungen sind dabei hartanodisierbar – aber je reiner die Legierung ist, umso mehr Oxide können gebildet werden. Auf sehr reinen Legierungen können daher Schichtdicken von bis zu 200 µm erreicht werden.
Hartanodische Schichten sind dabei wesentlich dichter und sehr viel härter als normale anodische Schichten: Die erzielbaren Schichthärten, die von der jeweils verwendeten Aluminiumlegierung abhängig sind, bewegen sich hier zwischen 350 und 600 HV.
Harteloxalschichten werden zu technischen Zwecken eingesetzt, beispielsweise für Bolzen, Lager, Gehäuse, Führungen, Steuerventile, Steuerkolben, Zahnräder, Schnecken und Aluminium-Profile. Der Vorteil der Harteloxalschichten liegt darin, dass Sie leichtere Werkstoffe einsetzen können, wenn Sie nicht eine bestimmte Grundfestigkeit und Zähigkeit des Werkstoffes benötigen. Und trotzdem können Sie damit extrem gute Verschleiß- und Korrosionsschutzwerte erreichen.
Fazit
Es gibt zahlreiche Verfahren um Oberflächen von Bauteilen zu schützen, zu veredeln oder zu vergüten. Diese dienen dazu, die Funktionseigenschaften während der Einsatzzeit sicherzustellen. Wie wir dargestellt haben, können Sie dabei durch die Auswahl einer geeigneten Beschichtung, Passivierung oder Deckschicht unterschiedliche Anforderungen erfüllen. Einen erforderlichen Korrosionsschutz müssen Sie z.B. bereits im Rahmen der Konstruktion durch eine entsprechende konstruktive Gestaltung sowie eine geeignete Auswahl der Werkstoffe berücksichtigen.
Neben wichtigen Umweltaspekten sowie gesetzlichen Bestimmungen ist es aber gleichermaßen ebenso immer auch eine Kostenfrage, für welche Art der Oberflächenbehandlung Sie sich entscheiden.
Das könnte Sie auch interessieren:
Kommentieren