Couplings and Coupling Systems – Requirements, Selection and Design
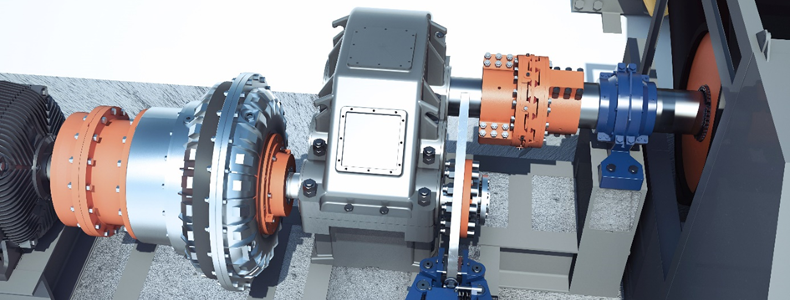
Torsionally Flexible Couplings
Torsionally flexible couplings are non-shiftable couplings which primarily serve to transmit torque. In addition to reliable torque transmission, the capability to compensate for shaft misalignments which often do not occur until on-site operation, presents another key aspect for the coupling selection. The distinction is made between angular, radial and axial shaft misalignments which have to be accommodated within predefined ranges.
![]() |
![]() |
![]() |
Angular Misalignment | Radial Misalignment | Axial Misalignment |
On top of that, by suitably selecting the elastomeric coupling elements, the natural frequencies of the drive line can be moved to an uncritical speed range so that the torsionally flexible coupling provides for the compensation of torsional vibration amplitudes and shock torques. For this reason, stiffness and damping characteristics are also essential parameters when designing a torsionally flexible coupling.
Design Criteria in View
The layout design of a torsionally flexible coupling must take size-dependent properties into account. These are, to begin with, the maximum drive torque, the maximum speed and, as the case may be, the required torsional stiffness and damping behavior. Nevertheless, plant-related parameters such as ambient temperatures and possible misalignment faults of the connecting shafts are of major importance, too.
Torque Calculation
The permissible coupling torque is of great significance to the design of the optimum coupling. The permissible torque is the maximum torque that may occur during operation. Apart from that, the coupling must be able to withstand the occurrence of particular and transient loads, for instance, at starts and stops, electrical or mechanical transfers, as well as, braking or accelerating maneuvers.
Stiffness Considerations
Stiffness is the ability of a body or material to resist elastic deformation caused by an external source such as torque or force. Notably with torsionally flexible couplings, torsional stiffness is a very important parameter. The stiffness depends on the elasticity of the material as well as on the form and size of the cross-section area of the body. The elastic properties of torsionally flexible couplings are greatly determined by elastomeric buffers being arranged in a ring inside the coupling.
The Challenge of Vibrations
If a system is periodically excited at a frequency that corresponds with the natural frequency of the system, the vibration amplitude will increase steadily. This is also referred to as “swing up”. If the vibrations are not attenuated, the amplitude continues to increase until the system will be destroyed – a so-called resonance catastrophe.
With a damping, which is mainly determined by the selected elastomer material, the vibration amplitude will assume a finite value. Such vibrations can, for example, be generated by a diesel engine of the reciprocating piston-and-cylinder type. The engine does not uniformly deliver its power during one revolution of the crankshaft: As a result, the torque being transferred into the drive on account of the combined action of the cylinders typically fluctuates strongly. These vibrations must be attenuated correspondingly during operation.
Temperature & Climate in the Focus
Another decisive parameter is temperature. Ambient temperatures and operation temperatures have a direct influence on the power transmission capability of the elastomer. Higher ambient temperatures will strongly influence the mechanical stability. These must be considered at an early design stage by using respective application factors in order to avoid possible impairment, premature failures and damage. If you use high-performance polyurethanes for the elastomeric buffers in torsionally flexible couplings, the influence of humidity will also play an important role.
For this reason, particular actions need to be implemented, if, for example, elastomeric couplings are used in the drive of a sugar mill that is operated in a tropical climate. In some cases, corrosion resistance is a requirement to be considered, so that a high-quality material has to be selected for the coupling parts. Alternatively, a suitable surface protection method such as nickel plating or electro-plating can be selected.
From the Standard to the Special Case
The mechanical design layout of couplings is defined in the standard DIN 740, Part 2. The calculation is usually done according to a standard procedure.
Torque is defined by the quotient from power and speed. Another criterion is the shaft diameter. The type and the configuration of the coupling are often determined by the installation conditions. If, for example, the driving and the driven machine are built into the same housing, the coupling must be of the plug-in type. In 80 % of the cases, the suitable coupling is then quickly found.
The remaining 20 % require a more precise calculation: These are often special applications which, for instance, require a high level of positioning accuracy. In torsionally flexible couplings, the coupling halves do not move simultaneously. However, this is not desired if high positioning accuracy is needed. The challenge here is to select the correct material. With increasing hardness, the positioning accuracy also increases – but this will adversely affect the damping properties. Iterative calculations then have to be conducted to find the optimum result.
Conclusion
Safe and reliable operation of a system can be achieved by tuning the dynamic behavior of the entire drive line. This includes the avoidance of resonance points within the operating range, the damping of vibrations and shock torques as well as the compensation of geometric misalignments. By keeping all these considerations in mind, you can prolong the service life of your entire plant.
Comment