Chemical Processes for the Surface Treatment of Components (2)
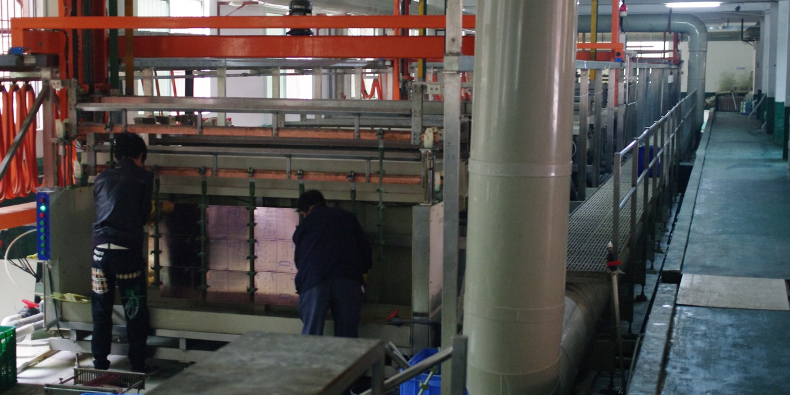
This is part 3 of our series on surface treatments of components. Due to the great number of different chemical processes, we have split them up and explored these processes in the previous article:
- Chromate conversion coating
- Phosphating
- Galvanizing
- Plating
- Black oxide.
This blog article covers the remaining chemical processes commonly applied for the treatment of component surfaces.
Chrome Plating
Chrome plating predominantly serves the purpose of corrosion protection and is categorized into decorative chrome plating, chrome electroplating and hard chrome plating.
Decorative chrome plating
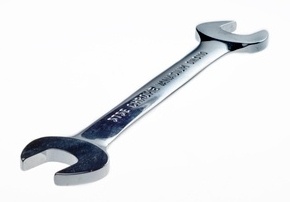
In this process, which is sometimes also called nickel-chrome plating, a very thin chromium layer is deposited which usually has a thickness of 0.2 to 0.5 µm.
Due to the slight thickness of such chrome layers, the gloss of the finished chrome-plated work piece is not only determined by the chrome layer itself, but also by the sub-layer which is typically a nickel layer.
Chrome electroplating
By using specific chemical additions and a higher current density, chrome layers of a deep black color deposit on the base metal. This black chrome layer is one of the few deep black surfaces that are electrically conductive.
Since the hardness of black chrome layers exhibits a range from only about 250 to 350 HV (Vickers Hardness or Vickers Hardness Number, VHN), they are less resistant to scratches and wear than, for example, decorative chrome coatings. This property can, however, be improved by treating the component with a special oil after the coating process. Black chrome plating is also used for decorative applications.
Hard chrome plating
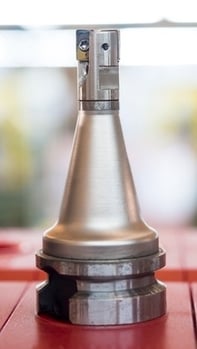
The denomination “hard chrome plating” is a bit confusing as it leads to the assumption that the hard chromium layer would be thicker than the (thinner) decorative chromium layer. In fact, however, it has almost the same thickness as the decorative chromium layer.
A normal decorative or hard chrome layer features a dense network of micro-cracks which is neither visible to the eye nor perceptible to the touch:
This “cracking nature” of chromium layers shows that a decorative chrome layer alone – in spite of its excellent properties – will not offer good corrosion protection. Therefore, reliable corrosion protection can only be achieved in combination with suitable intermediate layers (normally nickel or copper and nickel). In some applications, this crackly structure may even be advantageous as it provides for better adhesion of an oil film.
Cadmium Plating
Cadmium plating refers to the electro-deposition of a thin layer of cadmium on metals and offers excellent resistance to corrosion, especially in alkaline environments. The resistance properties of cadmium coatings are comparable to those of zinc layers. Cadmium layers can be chrome-plated, too. These coatings are mainly applied to bolts and other fasteners, because they eventually ensure constant tightening torques and ease of dismounting.
For this reason, cadmium is also used in specific applications in the aerospace, offshore, mining and nuclear power industries. On account of its high toxicity, there are other fields in which the use of cadmium is banned in Germany, e.g. for the surface coating of bolts or as an addition to paints. For the majority of application areas, however, adequate alternatives have been found, for example “zinc yellow passivated”.
Anodizing
Even though aluminum is a so-called base metal, it only reacts superficially with air and water on account of its passivation at room temperature. In order not to leave this process to chance, a layer of oxide is deposited on the aluminum by anodic oxidation. In contrast to electro-plating techniques, the protective layer is not deposited on the work piece, but an oxide or hydroxide is formed by conversion of the uppermost metallic layer.
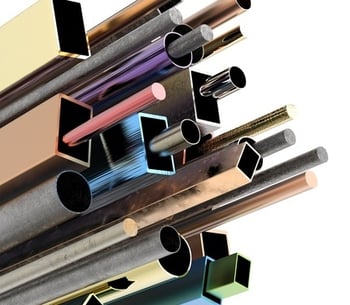
In this way, a layer ranging from 5 to 25 µm is built on the surface which protects the sub-layers against corrosion as long as no voids or holes are caused, for example, by mechanical damage. By comparison, the atmospheric oxide layer of aluminum – which is formed by natural oxidation – only has as a thickness of a few nanometers.
The oxide layers can be dyed in a variety of colors after the anodizing process, e.g. by dipping them into a hot paint solution (see above picture). Hardness values from 200 HV to 400 HV can be achieved by anodizing.
Hard Coating
Hard coating is also called “hard anodizing”. Similar to anodizing, the electrolytic oxidation of aluminum materials is used to produce a protective layer. This layer is resistant to wear and corrosion and, depending on the surface condition of the piece it is in contact with, offers good sliding properties which can even be improved with PTFE impregnation.
However, in contrast to anodizing, which is done at room temperature and with a relatively low current strength, the hard coating process is performed at very high current intensities. All aluminum alloys are suitable for anodizing, but the purer the alloy is, the more oxides can be formed. On very pure alloys, layer thicknesses of up to 200 µm can be deposited.
Hard anodized layers are considerably denser and much harder than normal anodic layers: Dependent on the aluminum alloy in question, hardness thicknesses ranging from 350 to 600 HV can be achieved.
Hard anodizing treatments are applied for technical purposes, for example for bolts, bearings, guides, control valves, pistons, gears, worms and aluminum profiles. The advantage offered by hard anodized layers is that you can use lighter materials, unless you need a certain basic strength and ductility of the material. Despite that, you can reach extremely good wear and corrosion protection properties.
Conclusion
There are many processes that protect, refine or improve the surfaces of components. They all serve to safeguard functional characteristics during the service life. As we explained, various requirements can be fulfilled by the selection of a suitable coating, passivation or top layer. The extent to which corrosion protection will be required must be clarified at an early design stage when determining the geometry of the article and selecting the materials.
Apart from environmental aspects as well as laws and regulations, when it comes to deciding which kind of treatment for you to use, the question of cost is always an important factor, too.
What might also be interesting for you:
Comment